ABS Injection Molding
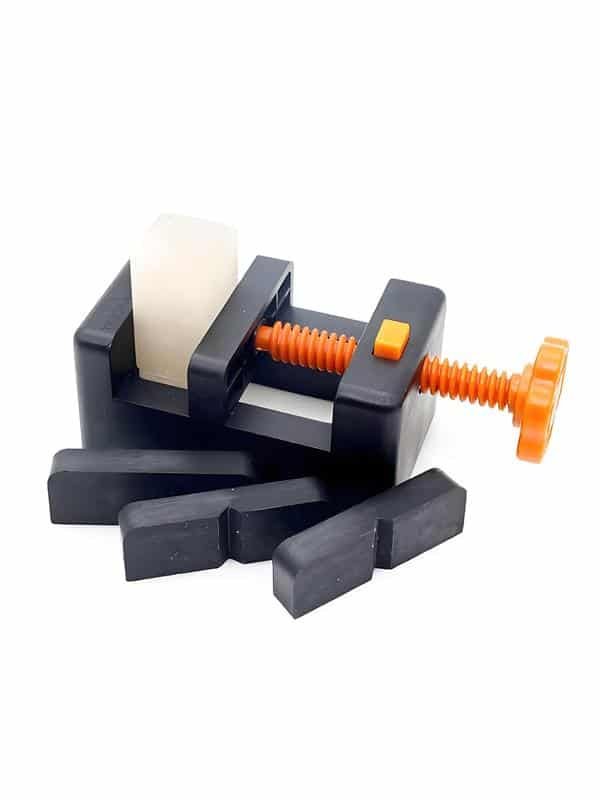
What is ABS Injection Molding?
Our ABS injection molding process starts with precision mold design, ensuring optimal part quality and consistency. We use advanced injection molding machines to efficiently melt and inject ABS plastic material into meticulously crafted molds. The material then undergoes controlled cooling and solidification, ensuring proper formation. Finally, professional finishing techniques guarantee durable, high-quality ABS components.
With expertise in mold fabrication, process optimization, and quality control, we deliver cost-effective, scalable solutions tailored to diverse industries. Whether you need custom molds or large-scale production, our strict quality standards and reliable manufacturing ensure top-tier results for your ABS plastic components.
Injection Molding ABS Parameters Table
Parameter | Recommended Range |
---|---|
Wall Thickness | 1.2mm-4mm |
Maximum Part Size | 2000mm x 1500mm x 1000mm |
Minimum Feature Size | 0.5mm-1mm |
Tolerances | ±0.05mm - ±0.2mm |
ABS Material Properties
ABS (Acrylonitrile Butadiene Styrene, Acrylonitrile Butadiene Styrene) is a kind of high performance thermoplastic, which is widely used in injection molding manufacturing because of its excellent strength, toughness and processability. It combines the advantages of three monomers:
- Acrylonitrile - which provides chemical resistance and hardness
- Butadiene - which provides excellent impact resistance and toughness
- Styrene - which gives ABS good rigidity, gloss and workability
Property | Density | Tensile Strength | Flexural Strength | Impact Strength (Unnotched) | Heat Deflection Temp (0.45 MPa) |
---|---|---|---|---|---|
Value/Description | 1.02-1.05g/cm³ | 40 -50 MPa | 60-70 MPa | 20 -30 kJ/m² | 90-100℃ |
- The above parameters represent the baseline performance of the materials. Actual application should be dynamically optimized based on specific working conditions.
Looking for High-Quality ABS Injection Molding?
Advantages & Disadvantages of ABS Injection Molding
Advantages
- High strength and toughness
- Good dimensional stability
- Excellent surface finish for painting or plating
- Cost-effective for mass production
Disadvantages
- Limited UV resistance
- Moderate heat resistance
- Can be prone to warping
Applications of Injection Molded ABS
Automotive Industry

- Dashboard components
- Interior trim pieces
- Bumper covers
- Grilles and lighting housings
Electronics Industry
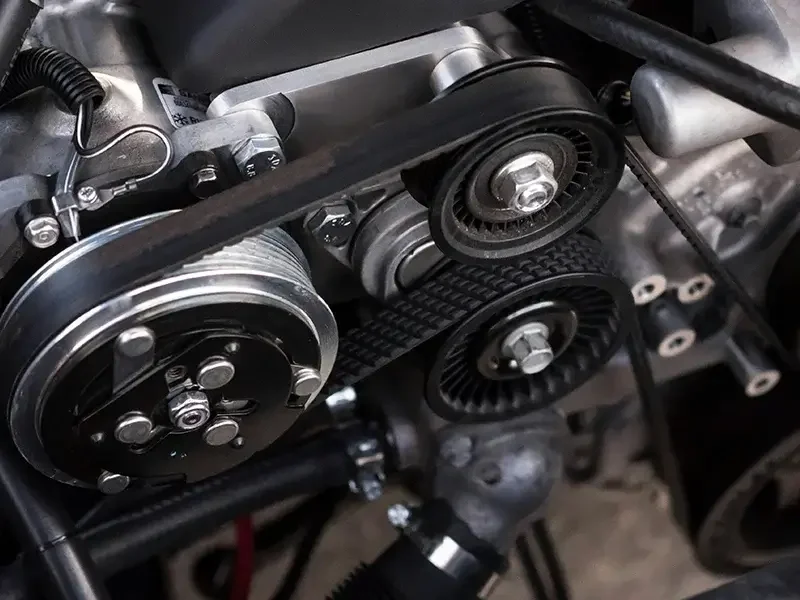
- Monitor housings
- Smartphone cases
- Keyboard keycaps
- Vacuum cleaner parts
Consumer Goods
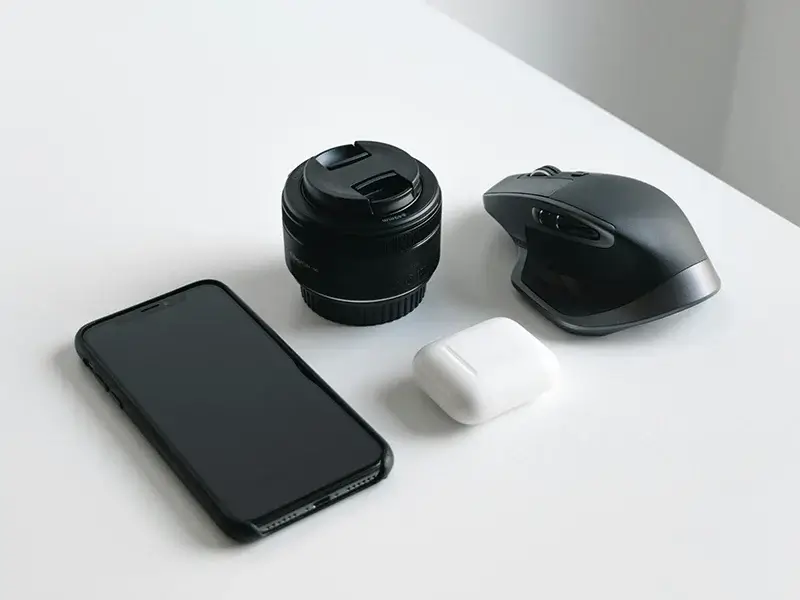
- Appliance housings
- Toys and games
- Sporting goods
- Daily necessities
Medical Devices
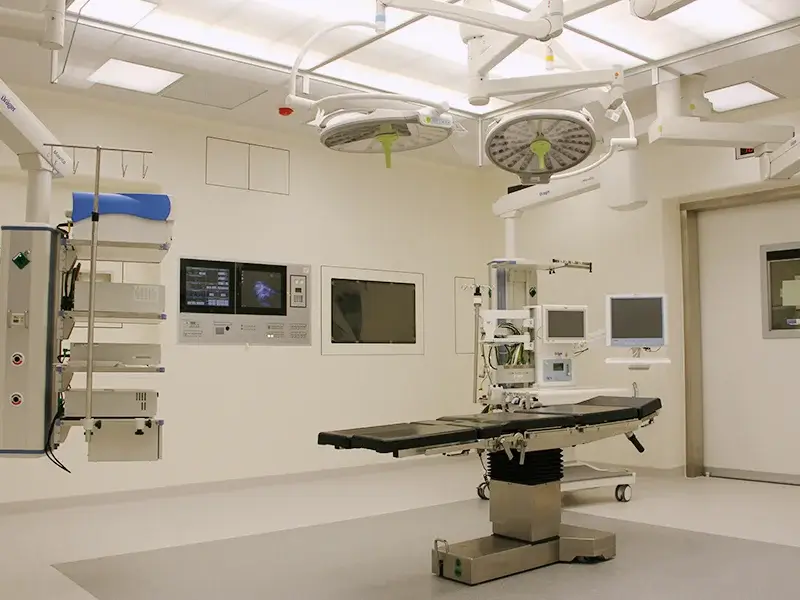
- Syringe components
- Inhalers and nebulizers
- Diagnostic equipment housings
- Contactless component
Jiangzhi ABS Injection Molding Parts is Guaranteed
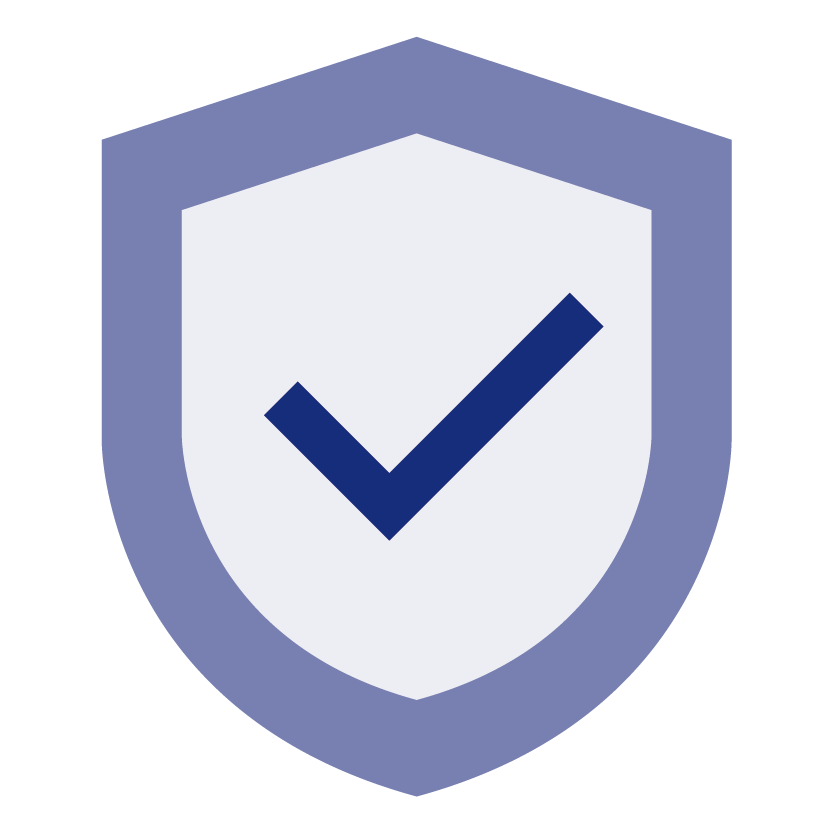
FAQs About Injection ABS Molding
ABS can break down if it gets too hot or stays in the barrel too long. This leads to discoloration, bad smells, or weaker parts. We avoid this by using the right temperature settings and proper cycle times.
Yes, ABS blends well with materials like PC (polycarbonate) to improve strength or heat resistance. But mixing must be done carefully to avoid compatibility issues. We’ll help you decide if blending makes sense for your project.
Cracks often come from stress during cooling, poor mold design, or even using the wrong processing temps. We focus on balanced part design and proper molding conditions to keep your ABS parts crack-free.
ABS runs well in molds made from hardened steel or aluminum, depending on your production volume. The key is smooth surfaces and good venting to avoid flow marks or burn spots.
ABS is stiffer and easier to paint or glue, while PP is more flexible and chemically resistant. ABS needs tighter temperature control, and PP shrinks more. Choosing between them depends on what your part needs to do—we’ll help you pick the best fit.