Injection Molding Material Selection Guide
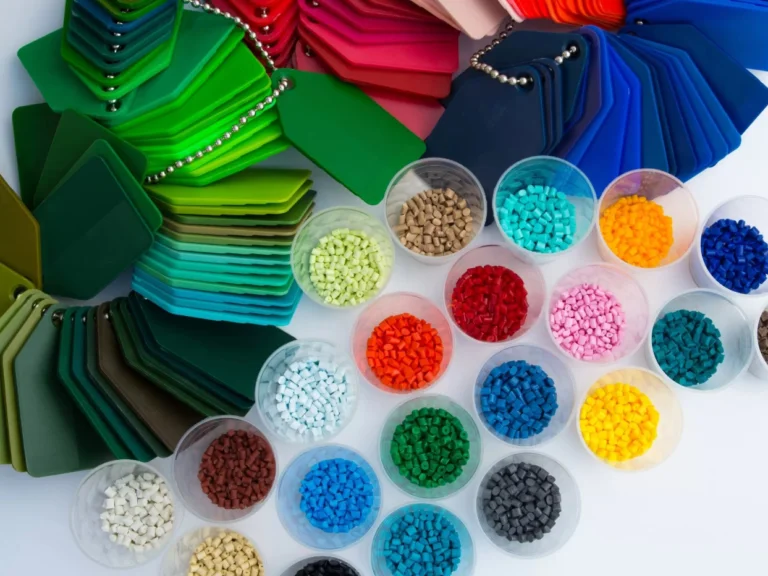
Choosing the right material for injection molding is critical to the success of any manufacturing project. The material impacts the product’s durability, performance, aesthetics, and cost. This comprehensive guide will help you navigate the complex process of plastic material selection for injection molding, ensuring your products meet all necessary requirements.
Injection Molding Material Selection Guide
Application Requirements
- Determine what is the end-use of the product.
- Identify environmental conditions, like working temperature, humidity, UV exposure, etc.
- Clarify mechanical properties needed, like strength, flexibility, hardness.
Consider Regulatory and Compliance Needs
- Consider industry-specific regulations, e.g., FDA for medical, RoHS for electronics.
- Ensure the material complies with relevant safety standards.
Aesthetic and Finish Requirements
- Decide on parts color, transparency, and surface finish.
- Consider any post-process treatments like painting or plating.
Cost and Availability
- Evaluate the cost of the material relative to the project budget.
- Consider the cost of processing material like cycle times and scrap rates.
Injection Molding Material Selection Guide
Selection of the right plastic material for injection molding is crucial to ensuring the final product meets functional, aesthetic, and regulatory requirements. To ensure optimal performance and durability of the final products, the following are the key criteria you can make informed decisions.
Mechanical Properties
Understanding the mechanical requirements of your product is vital. Consider factors such as tensile strength, flexibility versus rigidity, and impact resistance. The chosen material must withstand the forces it will encounter during use without deforming or breaking.
Thermal Properties
The material’s thermal properties are crucial, especially for products exposed to varying temperatures. Key factors include heat resistance, thermal stability, and thermal expansion. The material should maintain its integrity and performance across the operating temperature range.
Chemical Properties
The chemical environment in which the product will be used is another critical consideration. The material should exhibit resistance to chemicals, low moisture absorption, and oxidation resistance to prevent degradation and ensure longevity.
Electrical Properties
For applications involving electronics, electrical properties are essential. Materials should have the necessary insulation or conductivity characteristics to meet the specific requirements of the product, ensuring safety and functionality.
Injection Molding Material Selection Guide
Thermoplastic Polymer | Thermoset Polymer | |
---|---|---|
Description | Thermoplastics polymer is a polymer or plastic that can be melted and reshaped multiple times without losting their properties. | Thermosetting polymer is a polymer/plastic taht cannot be remolded once it is formed. |
Common Application |
|
|
Example Materials |
|
|
Pros |
|
|
Cons |
|
|
Injection Molding Material Plastic Selection Guide
Each of the plastic materials has unique properties that make them suitable for specific applications. This is an overview of common injection molding materials characteristics, strengths, and weaknesses.
1. Polypropylene (PP)
Polypropylene is a versatile thermoplastic polymer widely used in injection molding due to its balance of properties and cost-effectiveness.
Strengths: Good chemical resistance, high fatigue resistance, lightweight, low cost.
Weaknesses: Poor UV resistance, low thermal stability, susceptible to oxidation.
2. Acrylonitrile Butadiene Styrene (ABS)
ABS is a common thermoplastic polymer known for its strength and toughness, making it suitable for various applications.
Strengths: High impact resistance, good dimensional stability, excellent surface finish, easy to process.
Weaknesses: Poor UV resistance, limited chemical resistance, flammability.
3. Polyethylene (PE)
Polyethylene is a widely used polymer in different forms (HDPE, LDPE) known for its durability and versatility.
Strengths: Excellent chemical resistance, good impact resistance, low moisture absorption, low cost.
Weaknesses: Low strength and stiffness, poor UV resistance, limited high-temperature performance.
4. Polycarbonate (PC)
Polycarbonate is a strong, transparent thermoplastic with high impact resistance, commonly used for applications requiring clarity and toughness.
Strengths: High impact resistance, excellent transparency, good thermal stability, high dimensional stability.
Weaknesses: Susceptible to scratching, high cost, poor chemical resistance.
5. Polyamide (Nylon)
Nylon is a strong, wear-resistant thermoplastic used for applications requiring high mechanical strength and durability.
Strengths: High tensile strength, good wear resistance, excellent fatigue resistance.
Weaknesses: High moisture absorption, susceptible to hydrolysis, dimensional changes with humidity.
6. Polystyrene (PS)
Polystyrene is a versatile plastic with a wide range of uses, particularly in packaging and disposable products.
Strengths: Good clarity, easy to process, low cost.
Weaknesses: Brittle, poor chemical resistance, low impact resistance.
7. Polyethylene Terephthalate (PET)
PET is a strong, lightweight plastic widely used in beverage containers and food packaging.
Strengths: High strength, good thermal stability, excellent barrier properties.
Weaknesses: Limited impact resistance, higher processing temperature, susceptible to moisture absorption.
8. Thermoplastic Elastomers (TPE)
TPEs are flexible, rubber-like materials that combine the processing advantages of plastics with the elasticity of rubbers.
Strengths: High flexibility, good weather resistance, recyclable.
Weaknesses: Lower mechanical strength, limited chemical resistance, higher cost compared to traditional elastomers
Injection Molding Material Selection Guide
Additives play a vital role in enhancing the properties of injection molded plastics. They can improve performance, durability, and processing characteristics, making them indispensable in various applications. Below are some common additives used in injection molding materials:
Additives | Description |
---|---|
Plasticizers | Increase flexibility and reduce brittleness, enhancing the material's pliability for applications requiring flexibility. |
Stabilizers | Protect against degradation from heat, light, or oxygen, extending the material's lifespan by preventing discoloration and brittleness. |
Colorants | Provide desired color to the final product, enhancing aesthetic appeal and allowing for product differentiation. |
Reinforcements (e.g., glass fibers, carbon fibers) | Improve mechanical properties like strength and stiffness, increasing load-bearing capacity while reducing weight. |
Flame Retardants | Reduce flammability and enhance fire resistance, ensuring safety in applications where fire hazards are a concern. |
Antioxidants | Prevent oxidation and degradation during processing and use, maintaining material properties and extending product lifespan. |
UV Stabilizers | Protect against UV radiation damage, preventing discoloration, cracking, and loss of mechanical properties in outdoor applications. |
Antimicrobial Additives | Inhibit the growth of bacteria, fungi, and other microorganisms, enhancing hygiene and reducing contamination risks in medical and food-related applications. |
Impact Modifiers | Improve impact resistance and toughness, allowing the material to withstand shocks and impacts without cracking or breaking. |
Anti-static Agents | Reduce static electricity buildup, preventing dust attraction and static discharge, which is critical in electronic applications. |
Injection Molding Material Selection Guide
1. Define the requirements
- Identifies the nature of the application, environment, and working conditions.
- Clarifies factors like temperature, pressure, and corrosive elements are considered.
2. Identify potential materials
- Use material databased to filter options based on primary requirements.
- List potential materials that satisfy the given criteria is compiled.
3. Detailed evaluation and shortlist
- In-depth analysis to trim down the list of potential materials.
- Consider additional factors like cost and availability.
4. Prototype Testing
- Create prototypes using selected materials.
- Perform mechanical, thermal, and chemical tests.
5. Final Selection
- Analyze test results and feedback.
- Make a decision based on performance, cost, and availability.
Let Us Help You!
Available Processing Material
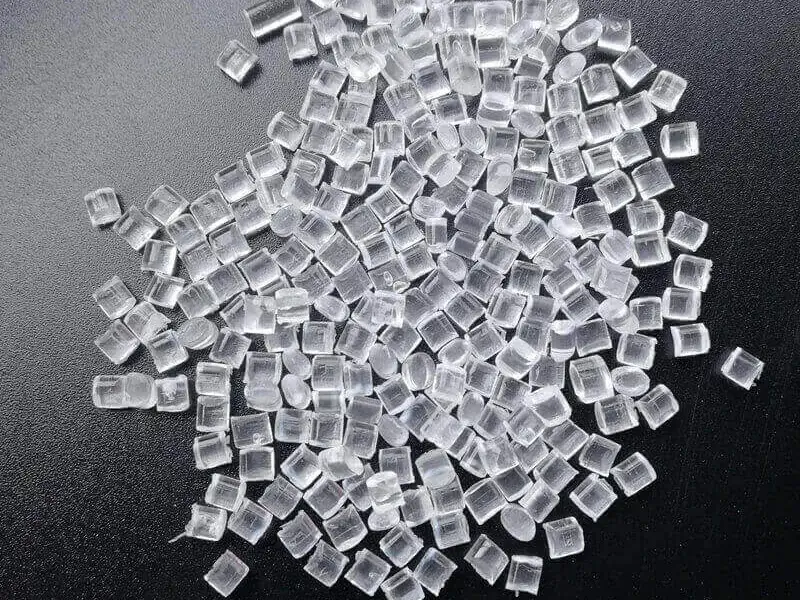
Plastic Material

Rubber Material
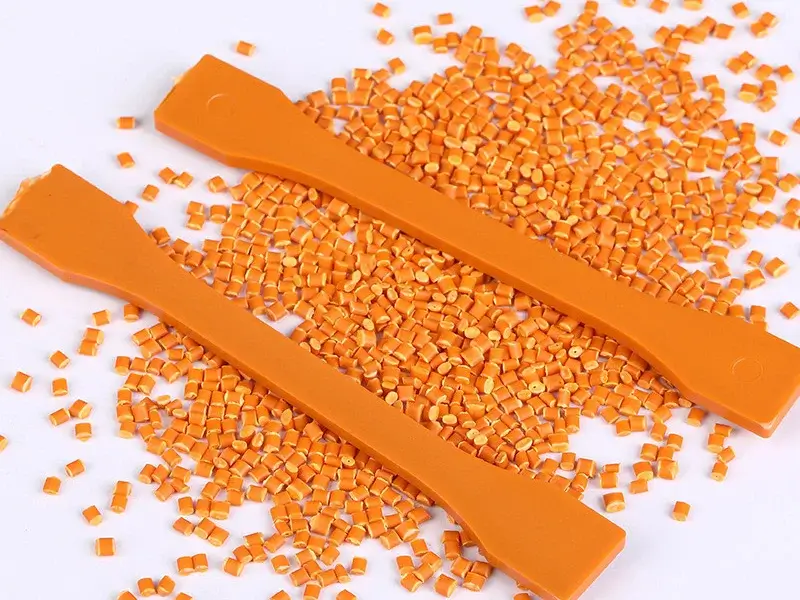
TPE Material
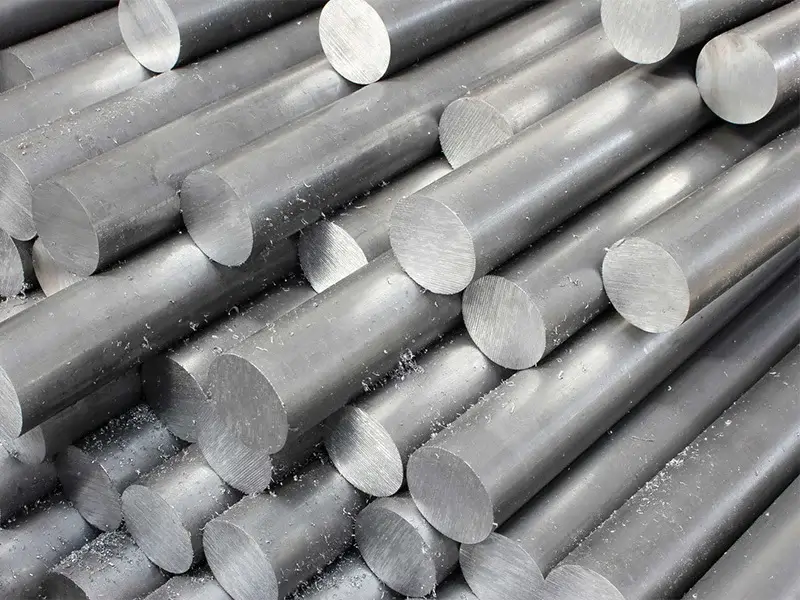