Custom Insert Molding Service
Enhance your products with our insert molding solutions services. We seamlessly integrate metal and plastic components, delivering durable, high-performance parts with precision and efficiency.
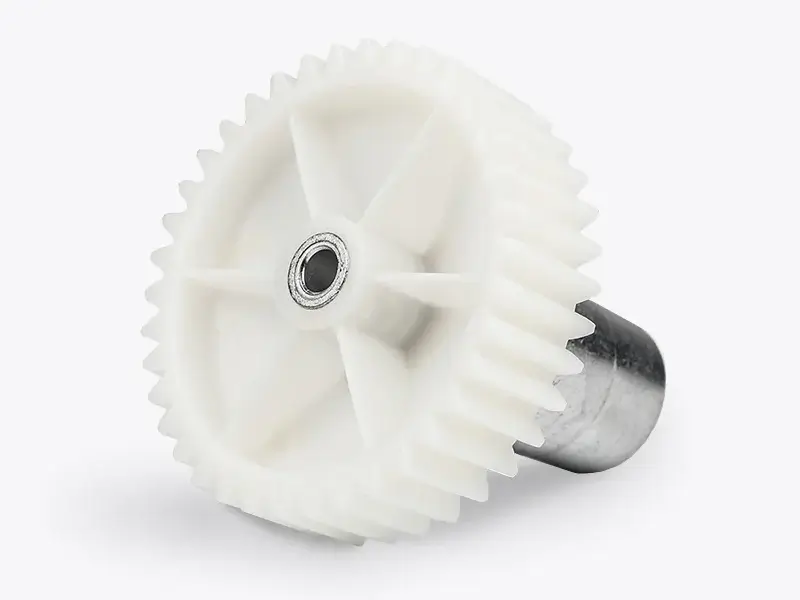

Jiangzhi provides custom insert molding services for both low-volume and high-volume production. Using advanced tooling, we seamlessly integrate metal inserts or other components into plastic parts, ensuring enhanced strength and durability. With competitive pricing and a variety of materials to choose from, our insert molding solutions are designed to meet your specific functional needs and budget.

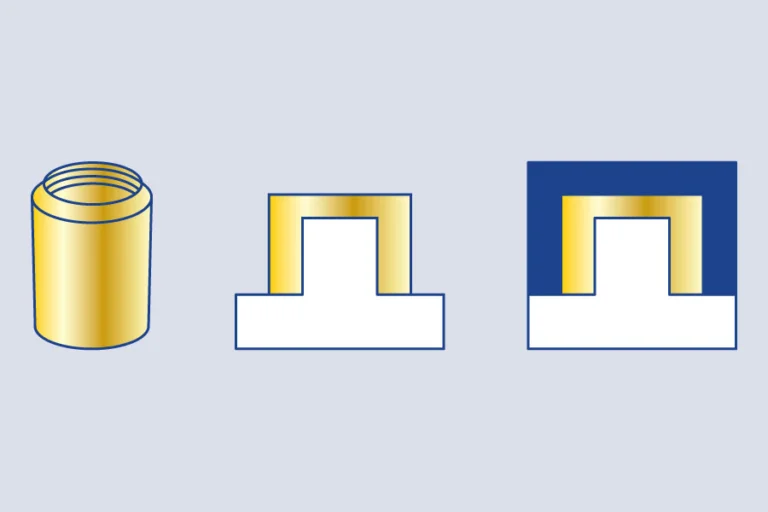
What Is Insert Molding Service?
Insert molding is an advanced injection molding process that combines metal, plastic, or ceramic components into a single, integrated part. By placing pre-formed inserts into a mold and overmolding them with plastic, insert molding creates strong, multifunctional components—while eliminating the need for secondary assembly or adhesives. This not only enhances structural integrity but also streamlines production and improves overall product performance.
At Jiangzhi, we specialize in custom insert molding services tailored to your exact requirements. Work with us to optimize your design, shorten your production timeline, and achieve greater product value—backed by decades of manufacturing experience and a commitment to quality.
Insert Molding Services Material
Inserts Molding Materials
The molding material or the resin is chosen based on the mold. We offer the following materials for insert molding process.
- Polypropylene (PP)
- Polyamides/Nylon (PA)
- Polycarbonate (PC)
- Acrylonitrile Butadiene Styrene (ABS)
- Polyethylene (PE)
- Polyurethane (PU)
- Natural Rubber (NR)
Insert Types
We offer various types of inserts for insert molded components. Metal inserts in plastic molding are typically made of brass, stainless steel, or standard steel.
- Custom insert for special need
- Screws and threaded fastener
- Electronics component
- Bearing and bushing
- Magnet
- Clip, pin, spring, and rivets
Injection Molding Material Selection Guide
How Does Insert Injection Molding Process Work?
Insert Preparation

- Metal inserts (e.g., brass, stainless steel, aluminum) require surface cleaning and may need preheating to reduce thermal shock.
- Plastic inserts (e.g., nylon or PC components) must be dry, clean, and dimensionally stable to ensure bonding and prevent deformation.
Insert Placement

- Inserts are manually or robotically positioned into mold cavities.
- Securing methods—like magnetic fixtures, vacuum suction, or tight-fitting pockets—ensure stability during injection, especially for heavier metal inserts.
Mold Clamping

- The mold is closed with inserts precisely aligned.
- Accurate clamping is critical to prevent shifting, particularly for metal parts due to their weight and thermal expansion.
Plastic Injection

- Molten thermoplastic is injected under high pressure to flow around and encapsulate the insert.
- Material compatibility is essential, especially when overmolding plastic inserts to avoid delamination or warping.
Cooling & Solidification

- The plastic cools and bonds with the insert.
- Metal inserts may extend cooling time due to heat retention, while plastic inserts require tighter control over shrinkage and bonding to avoid defects.
Cooling and Ejection

- Mold opens and parts are ejected carefully to protect the insert’s integrity.
- With both insert types, proper ejection design (e.g., ejector pin location) ensures the insert remains securely fixed in the molded part.
Customized Insert Molding Products
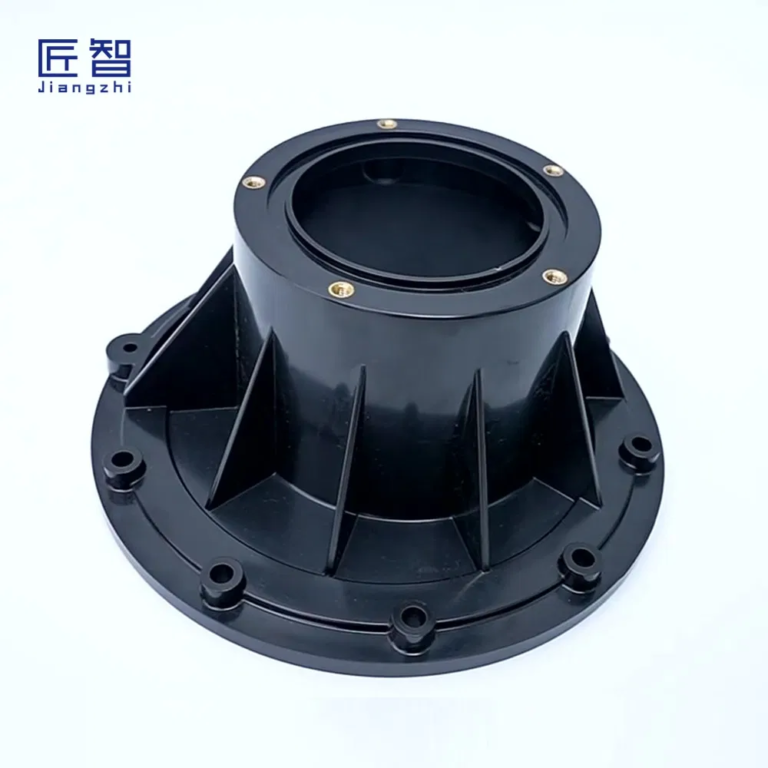
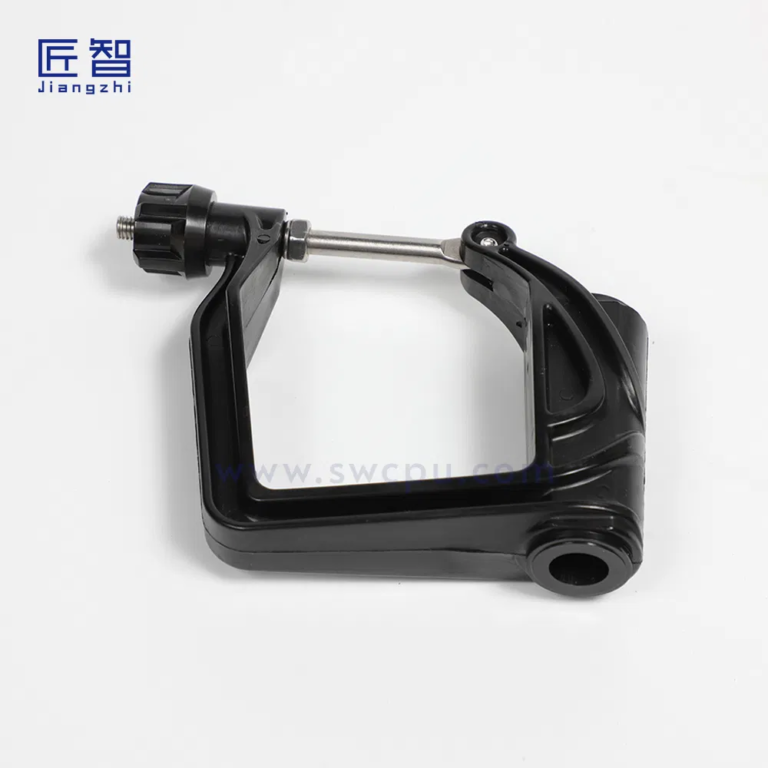






Advantages of Insert Molding Process
- Combines multiple functions in one part
- Eliminates need for secondary assembly steps
- Enhances part durability, strength, and appearance
- Compatible with various insert types and shapes
- Reduces overall manufacturing cost
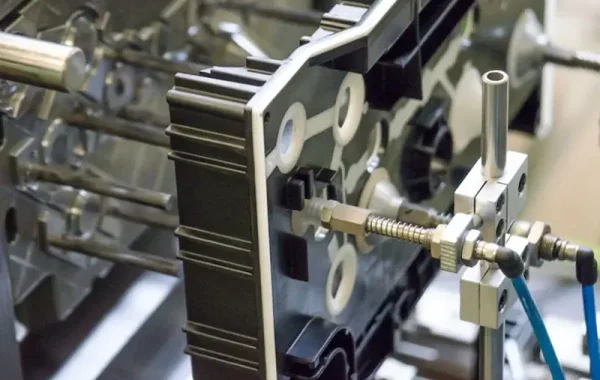
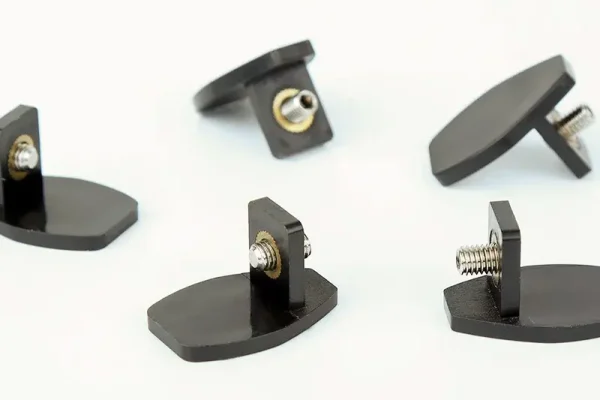
Application of Insert Molding Service
- Electrical Connector
- Auto Instrument panel group
- Car Seat Parts
- Medical Catheters and Fittings
- Insert Molded Housings
- Computer Accessories
- Fasteners and threaded parts
Metal & Plastic Insert Molding Components Application
Why Choose Us?
Ensuring accurate and intricate part production
Meeting diverse industry needs
Proven track record in successful projects
Rigorous quality checks for reliable results
Professional Injection Molding One-Stop Service Company
Improve production efficiency and choose efficient insert injection molding solutions!
FAQs of Insert Molding
How does plastic insert molding improve productivity?
By integrating inserts with plastic parts, insertion molding eliminates assembly steps and improves production efficiency, especially for mass production.
What inserts can I use for custom insert molding service?
Inserts can be metal (such as steel, aluminum, copper), ceramic, or hard plastics, depending on the strength, corrosion resistance, and other requirements of the final product. Don’t know how to choose, let the Jiangzhi to help you!
How long is the production cycle of insertion molding?
The production cycle of custom insert molding depends on several factors, such as mold complexity, part size, and production volume. Generally speaking, The single production cycle of insert molding is usually between 1 and 5 minutes, but this also needs to be adjusted according to the specific production conditions. In mass production, the cycle may be shorter, because the mold and equipment have entered a stable working state.
Does the insert move during insertion molding?
Is the insertion firmly attached to the plastic? Is there a risk of falling off?
In the Insert Molding process, the attachment of the insert to the plastic is usually very strong. By precisely controlling the mold temperature, injection pressure and cooling rate, we are able to ensure a strong bond between the insert and the plastic. To ensure the highest quality, we carry out rigorous quality testing on each product, including strength testing, adhesion testing and dimensional accuracy checks to eliminate the risk of falling off.
What are the similarities and differences between overmoulding and insert moulding?
Overmoulding involves injecting a material over an existing part to add a new layer, while insert moulding embeds a pre-made component, like metal, into a plastic part. Both processes combine materials to enhance functionality, but overmoulding adds a soft or protective layer, and insert moulding integrates parts for added strength or features. Learn more about insert and overmolding details.