Steel CNC Machining Service
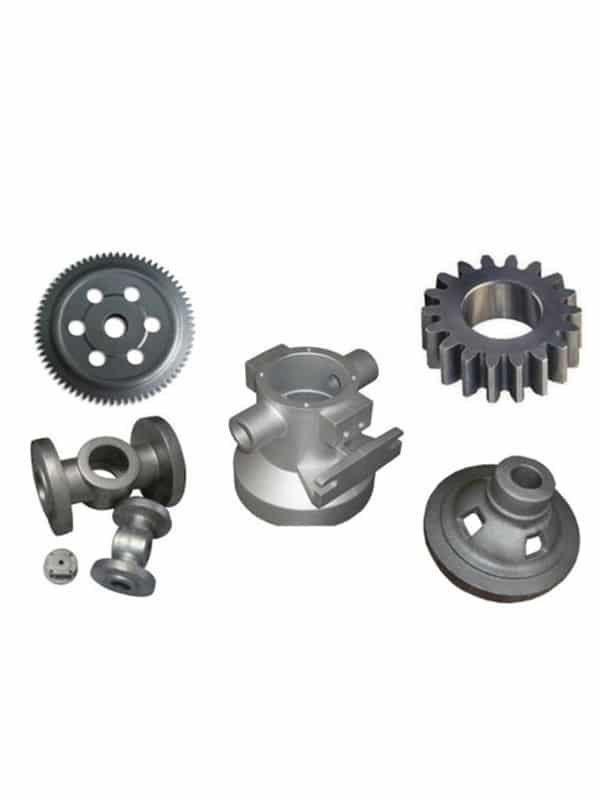
CNC Machining in Steel Material
At Jiangzhi, we focus on high-precision steel CNC machining, delivering dependable solutions for both prototype development and small-scale production. Leveraging our state-of-the-art multi-axis CNC equipment and skilled machinists, we consistently achieve tight tolerances, repeatable quality, and excellent surface finishes based on your detailed CAD drawings or 2D files.
As an experienced steel machining company, we work with a wide range of CNC machined steel materials, including carbon steel, alloy steel, and stainless steel. These machined steel parts are widely used in industries such as automotive, heavy machinery, oil and gas, and industrial automation. From design validation to on-time delivery, we help bring your parts to life accurately, efficiently, and cost-effectively.
Price | $$$ |
---|---|
Tolerances | ±0.01mm |
Maximum Part Size | 1000mm x 800mm x 400mm |
Minimum Feature Size | Φ 0.8mm |
Wall Thickness | 1.0mm |
Lead Time | About 3-6 days |
Machining Properties of Steel
Steel is a versatile and widely used material in CNC machining due to its excellent mechanical properties and broad range of grades. Compared to softer metals like aluminum, steel generally requires more careful control of cutting parameters because of its higher hardness and strength. Its machinability varies widely depending on the alloy composition, heat treatment, and microstructure, impacting cutting speed, tool wear, surface finish, and dimensional accuracy. Common types of steel used in CNC machining include:
- Carbon Steel – Offers a good balance of strength and machinability, suitable for structural components and general-purpose parts.
- Alloy Steel – Contains additional alloying elements that improve strength, toughness, and wear resistance, often requiring specialized tooling and slower feeds.
- Stainless Steel – Known for corrosion resistance but is more difficult to machine due to work hardening; requires careful tooling and coolant management.
- Tool Steel – High hardness and wear resistance make it ideal for cutting tools and dies, but it is challenging to machine and often requires slower cutting speeds.
- Maraging Steel – Ultra-high strength steel with excellent toughness, commonly used in aerospace and tooling applications, demanding precise machining parameters.
Tensile Strength (MPa) | Hardness (HB) | Elongation at Break (%) | Thermal Conductivity (W/m·K) | Corrosion Resistance | Melting Point (°C) | CNC Machining Notes |
---|---|---|---|---|---|---|
400–1200 | 120–300 | 10–40 | 15–50 | Poor to Moderate (needs coating) | 1370–1510 | Moderate machinability; use proper tooling and coolant; control heat and tool wear |
- The above parameters represent the baseline performance of the materials. Actual application should be dynamically optimized based on specific working conditions.
Get Custom CNC Steel Parts Now
Advantages & Disadvantages of Steel CNC Service
Advantages
- High strength and toughness – ideal for structural and load-bearing parts
- Cost-effective – widely available and competitively priced
- Easy to weld and heat-treat – adaptable to different applications
- Suitable for large parts – great for industrial equipment and heavy-duty use
Disadvantages
- Low corrosion resistance – requires protective coating (e.g., painting, plating)
- Higher tool wear – especially with harder grades
- Prone to oxidation – must be stored and handled properly
- Requires post-processing – deburring and surface treatment usually needed
Get Custom CNC Steel Parts Now
Standard finish with visible tool marks; suitable for functional prototypes and internal components.
Uses abrasive media to create a uniform matte or satin finish; also improves coating adhesion on plastic or metal surfaces.
Adds logos, text, or identification marks via silk screen or pad printing, ideal for branding or part tracking.
Removes machining marks and evens out surface texture; ideal for prototypes and parts where appearance is not critical.
Painting and powder coating provide colorful, durable, and corrosion-resistant finishes.
Deposits metal layers such as nickel or chrome on parts, improving wear resistance, conductivity, and aesthetic quality.
Produces a smooth, glossy finish; commonly applied to plastics like PC or PMMA for enhanced clarity and premium look.
Chemical treatment for ferrous metals, creating a dark, corrosion-resistant surface with minimal thickness.
Electrochemical process for aluminum that enhances corrosion and wear resistance, with options for colored finishes.
Jiangzhi CNC machined Steel Parts Machining Are Guaranteed
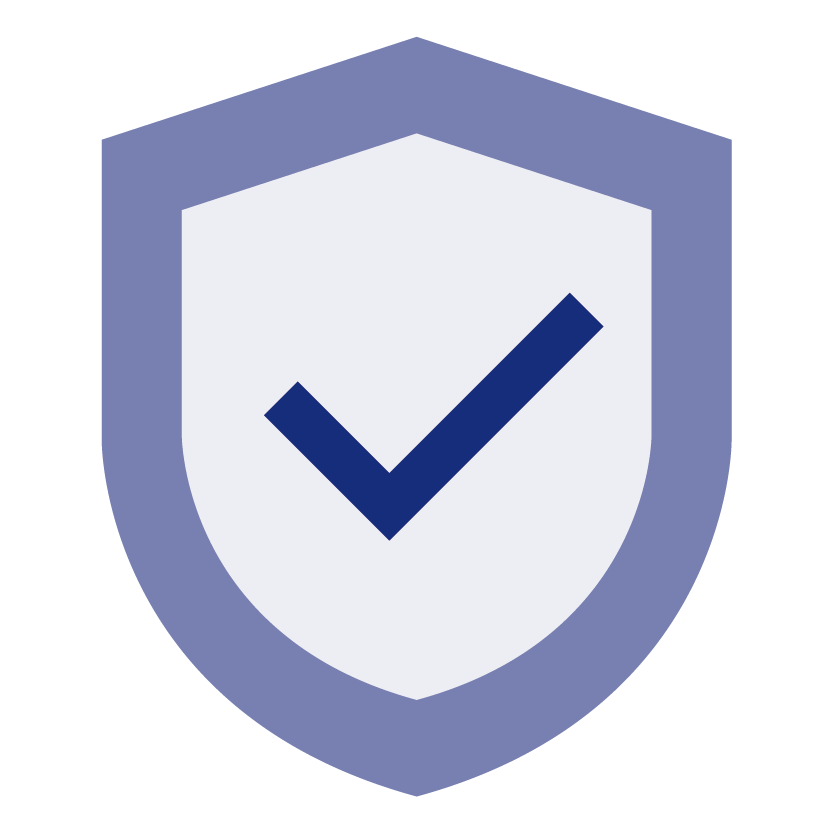
FAQs About Steel CNC Machining
Steel has a relatively high hardness, which can easily lead to tool wear and overheating during processing. Therefore, wear-resistant tools need to be used and the cutting speed and coolant should be controlled.
Carbon steel is generally easier to machine and weld, suitable for structural and general-purpose parts. Alloy steel offers higher strength and wear resistance but may require specialized tooling and machining parameters.
It is necessary to consider reasonable wall thickness, avoid sharp inner corners, chamfer design that is convenient for cutting, and ensure the structural rigidity of the part to reduce deformation.
Often yes, especially for carbon and alloy steels which can corrode. Common finishes include black oxide, powder coating, zinc plating, or passivation for stainless steel to improve corrosion resistance.
Absolutely. We review your files and provide expert feedback to ensure your CNC carbon steel parts are manufacturable and cost-efficient.