Polycarbonate Injection Molding
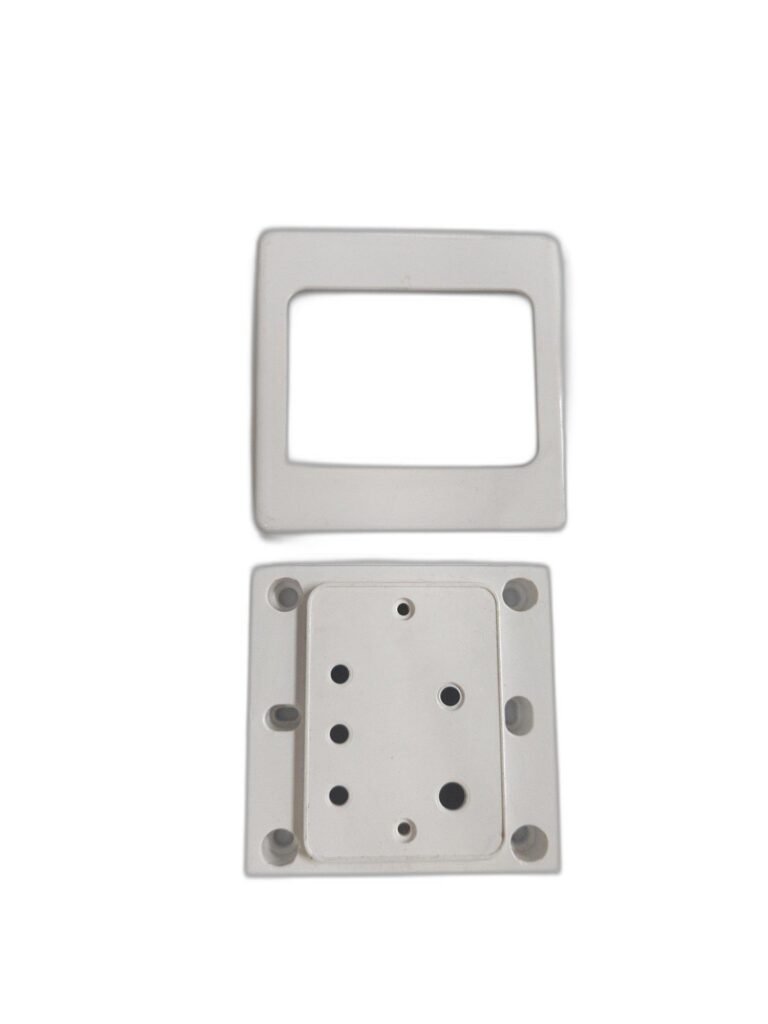
What is Polycarbonate Injection Molding?
Our polycarbonate plastic molding process ensures high precision and durability, utilizing advanced molding technology to shape polycarbonate into complex, high-quality components.
- The process starts with meticulous mold design, ensuring accuracy and repeatability.
- High-temperature processing is used to melt and inject PC resin into custom molds.
- A controlled cooling cycle ensures optimal material properties, such as impact resistance and clarity.
- Finally, post-processing techniques, including polishing and coating, enhance durability and aesthetics.
With extensive expertise in mold fabrication, material optimization, and quality control, we provide cost-effective, scalable solutions tailored to industries requiring transparent, impact-resistant, and heat-stable polycarbonate moulding components.
Injection Molding PC Parameters Table
Parameter | Recommended Range |
---|---|
Wall Thickness | 1.2mm-4mm |
Maximum Part Size | 2000mm x 1500mm x 600mm |
Minimum Feature Size | 0.2mm-0.8mm |
Tolerances | ±0.02mm - ±0.1mm |
PC Material Properties
PC (Polycarbonate) is a high-performance thermoplastic known for its exceptional impact resistance, optical clarity, and heat stability. Its unique molecular structure allows it to be lightweight yet highly durable, making it ideal for demanding applications. Key Material Properties:
- High impact resistance – withstands significant mechanical stress
- Superior optical clarity – excellent for transparent and translucent components
- Good dimensional stability – maintains precision in high-temperature environments
- Flame retardant – commonly used in electronics and safety equipment
Property | Density | Tensile Strength | Flexural Strength | Impact Strength (Unnotched) | Heat Deflection Temp (0.45 MPa) |
---|---|---|---|---|---|
Value/Description | 1.18 - 1.22g/cm³ | 55 - 75 MPa | 80 -110 MPa | 60 - 80 kJ/m² | 125 - 135℃ |
- The above parameters represent the baseline performance of the materials. Actual application should be dynamically optimized based on specific working conditions.
Looking for High-Quality Polycarbonate Molding?
Advantages & Disadvantages of PC Injection Molding
Advantages
- High impact resistance – withstands drops and mechanical stress
- Excellent transparency – ideal for optical and lighting applications
- Good heat resistance – suitable for high-temperature environments
- Flame-retardant grades available – used in electronics and safety gear
Disadvantages
- Susceptible to UV degradation – may require UV stabilization
- Prone to stress cracking – proper design considerations are needed
- Higher processing temperature – requires specialized molding expertise
Applications of Injection Molding Polycarbonate
Injection molding polycarbonate is widely used across industries due to its strength, transparent injection molding capabilities, and heat resistance. Our expertise in clear plastic molding ensures high optical clarity and precision for clear plastic injection molding applications.
Automotive Industry

- Headlamp lenses
- Instrument panels
- Interior trim components
- Safety shields
Electronics Industry

- LED light covers
- Transparent display panels
- Protective casings
- Electrical enclosures
Consumer Goods
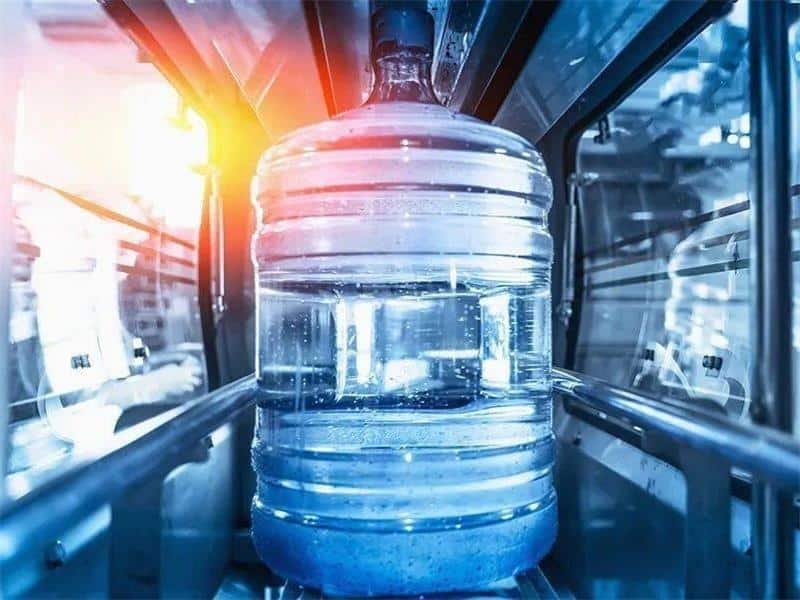
- Sports eyewear lenses
- Transparent protective covers
- High-durability cases
- Water dispenser parts
Medical Devices
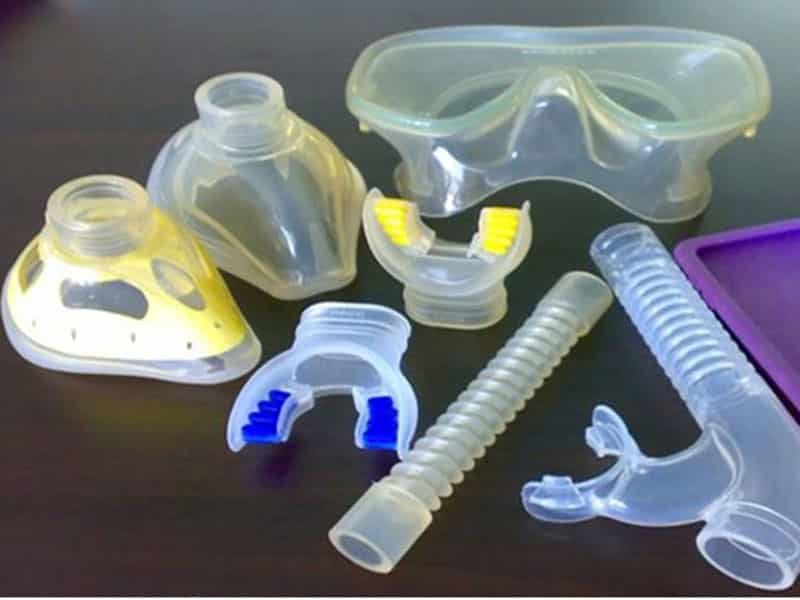
- Surgical instrument housings
- Protective face shields
- Transparent medical enclosures
- Lab equipment components
Jiangzhi PC Injection Molding Parts are Guaranteed
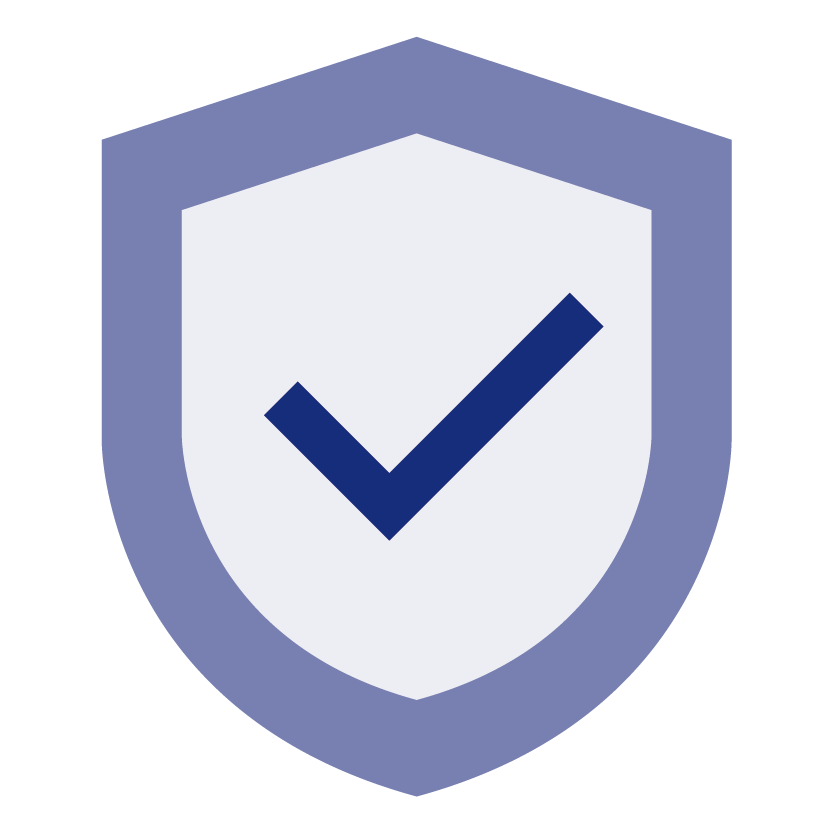
FAQs About Injection Molding Polycarbonate
- High processing temperature requirements
- Susceptibility to scratching without protective coatings
- Prone to moisture absorption, requiring proper drying before molding
- High viscosity, which may require increased injection pressure
Yes, PC can be overmolded with compatible materials like TPE (Thermoplastic Elastomer) or ABS for improved functionality and aesthetics.
- PC vs. PMMA (Acrylic): PC is more impact-resistant but less scratch-resistant. PMMA offers better clarity and UV resistance.
- PC vs. PETG: PC is stronger and more heat-resistant, while PETG is easier to process and lower in cost.
The cost depends on factors like part complexity, mold design, production volume, and finishing requirements. Generally, PC is more expensive than standard plastics like PP or ABS but provides superior properties.