PS Injection Molding
Custom Polystyrene Molding for High-Precision, Cost-Effective Plastic Parts. Achieve crisp finishes and excellent dimensional stability with our PS injection molding services. Ideal for medical, electronics, and consumer goods.
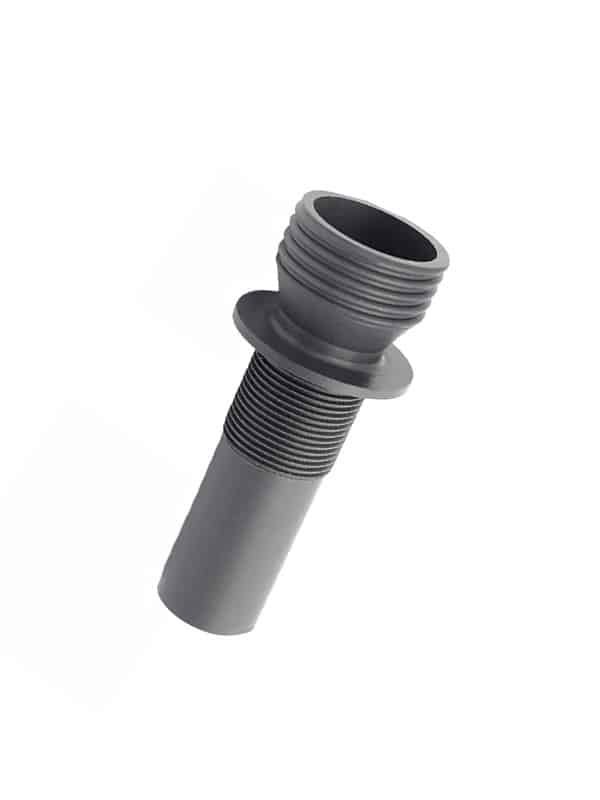
What is PS Injection Molding?
PS (Polystyrene) injection molding is a highly efficient and cost-effective manufacturing process used to produce high-precision plastic parts with excellent clarity, dimensional stability, and rigidity. It is particularly suited for components that require a clean surface finish, tight tolerances, and optical performance.
- Mould Design: PS moulding design emphasizes uniform wall thickness and sharp details to avoid sink marks and ensure visual consistency.
- PS Injection Process: Polystyrene pellets are melted and injected into custom molds at relatively low processing temperatures, allowing for smooth flow and fast cycle times.
- Cooling & Ejection: Rapid cooling is managed to maintain dimensional accuracy and reduce internal stress, especially for transparent parts.
- Post-Processing: PS molded parts may undergo secondary operations like printing, coating, or ultrasonic welding to meet design and branding needs.
At Jiangzhi, we utilize optimized gating systems, venting designs, and surface finish controls to deliver polystyrene molded parts with high consistency and optical quality. Our PS injection molding solutions offer the consistency and scalability required for consumer, medical, and industrial markets.
PS Injection Moulding Parameters Table
Parameter | Recommended Range |
---|---|
Wall Thickness | 0.8mm - 4.0mm |
Maximum Part Size | 1200mm x 1000mm x 500mm |
Minimum Feature Size | 0.5mm - 1.0mm |
Tolerances | ±0.05mm - ±0.2mm |
PS Material Properties
Polystyrene (PS) is a cost-effective thermoplastic known for its rigidity, optical clarity, and ease of processing. It exists in two major forms:
- GPPS (General PurposePolystyrene) – Transparent, brittle, ideal for clear housings and packaging
- HIPS (High Impact Polystyrene) – Opaque, impact-modified, ideal for durable enclosures and functional parts
Property | Density | Tensile Strength | Flexural Strength | Impact Strength (Unnotched) | Heat Deflection Temp (0.45 MPa) |
---|---|---|---|---|---|
Value/Description | 1.04 - 1.08g/cm³ | 35 - 55 MPa | 65 - 95 MPa | 1 -10 kJ/m² | 70 - 100℃ |
- The above parameters represent the baseline performance of the materials. Actual application should be dynamically optimized based on specific working conditions.
Want Clear, Lightweight Polystyrene Parts?
Advantages & Disadvantages of PS Injection Molding
Advantages
- High Clarity & Smooth Surface: Ideal for transparent or decorative parts
- Cost-Efficient: Lower material and tooling costs compared to engineering plastics
- Excellent Moldability: Short cycle time, easy to shape and detail
- Recyclable: Supports sustainable manufacturing processes
Disadvantages
- Brittle Without Modifiers: Not suitable for high-impact environments (GPPS)
- Low Heat Resistance: Deforms under continuous high temperatures
- Limited Chemical Resistance: Vulnerable to certain solvents and oils
Applications of Injection Molded PS Plastic
Consumer & Packaging
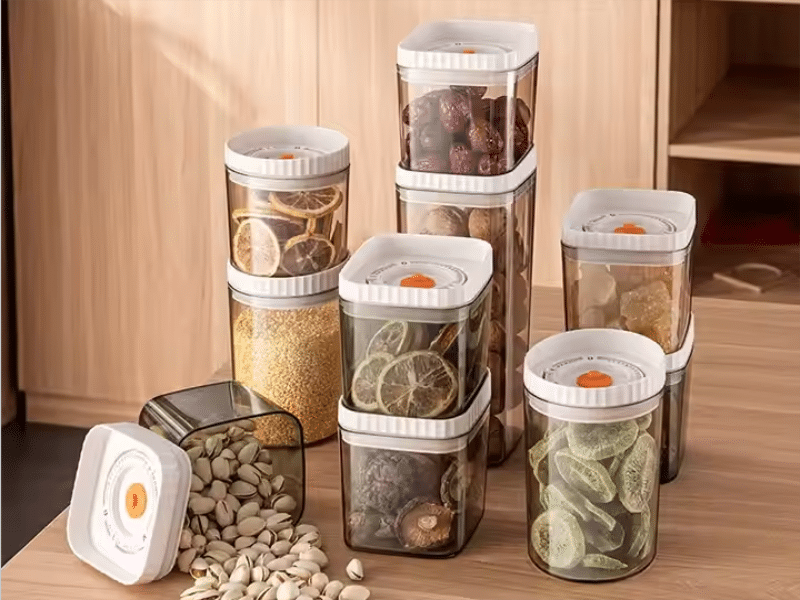
- Transparent casings
- Cosmetic containers
- Display trays
- Toy shells
Electronics & Appliances

- Housings for small devices
- Fan grills
- Switch covers
- Refrigerator line
Medical & Laboratory Use

- Disposable test tubes
- Petri dishes
- Syringe bodies
- Packaging for sterile tools
Retail & Display

- Point-of-sale stands
- Custom hangers
- Signage bases
- Light diffusers
Jiangzhi PS Injection Molding Parts are Guaranteed
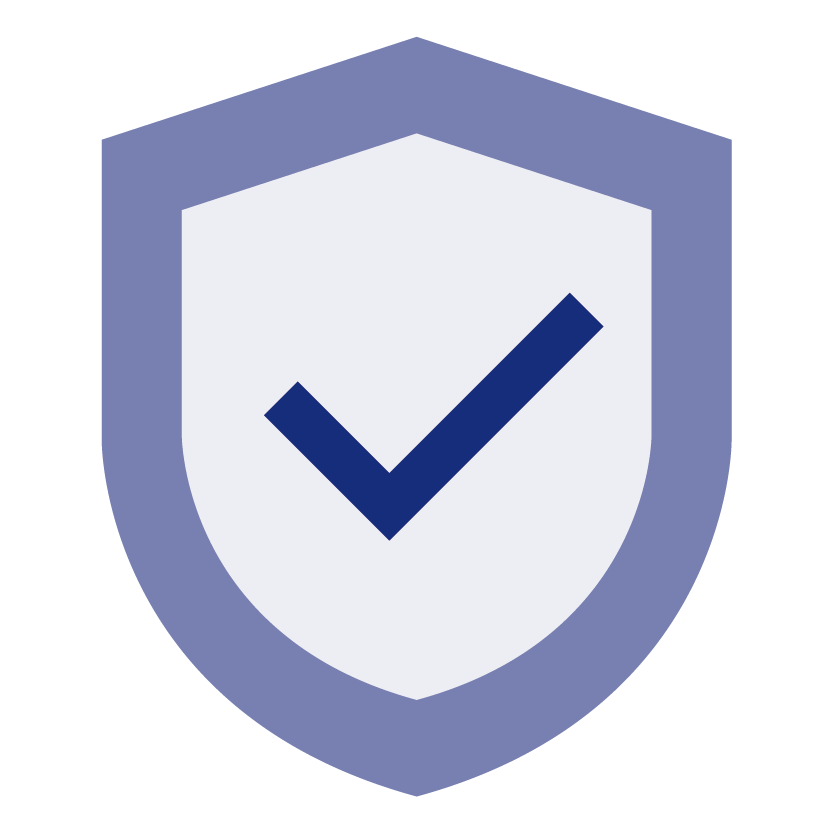
FAQs About Injection PS Molding
PS vs. ABS: PS is clearer but less impact-resistant than ABS
PS vs. PP: PS has better rigidity and dimensional accuracy, while PP is more flexible and chemical-resistant
PS is one of the most economical thermoplastics. Costs depend on mold complexity, part size, and production volume. GPPS is usually cheaper than HIPS.
- Brittleness or cracking: Caused by sharp corners or improper material handling
- Flow marks or weld lines: Due to low injection speed or cold mold
- Sink marks: Caused by uneven wall thickness
- Avoid sharp corners to reduce stress
- Maintain uniform wall thickness
- Include draft angles for easier part ejection
- Consider ribbing for structural strength