PVC Injection Moulding

What is PVC Injection Molding?
PVC (Polyvinyl Chloride) injection moulding is a precise and cost-efficient process used to produce complex plastic components with superior chemical resistance, electrical insulation, and flame retardancy. Whether it’s rigid or flexible, injection molded PVC is ideal for custom parts across a wide range of industries.
- Mould Design: Tailored PVC moulding design ensures accurate cavity geometry and accommodates the material’s flow behavior.
- PVC Injection Process: The process melts PVC granules and injects them into a temperature-controlled mold using low shear speeds to avoid degradation.
- Cooling & Ejection: Carefully regulated cooling minimizes warpage and optimizes dimensional stability.
- Post-Processing: Molding PVC plastic may include treatments like printing, texturing, or bonding for enhanced functionality.
We provide comprehensive support from PVC moulding design to PVC molding production, ensuring reliable and scalable solutions for your project.
Parameter | Recommended Range |
---|---|
Wall Thickness | 1.0mm - 6.0mm |
Maximum Part Size | 1500mm x 1000mm x 600mm |
Minimum Feature Size | 0.5mm - 1.0mm |
Tolerances | ±0.05mm - ±0.20mm |
PVC Material Properties
Injection molded PVC (Polyvinyl Chloride) is available in both rigid and flexible forms. Known for its chemical resistance, self-extinguishing nature, and cost efficiency, PVC plastic molding is widely used in applications requiring insulation, strength, and durability. Key Material Properties:
- Chemical resistance – withstands acids, alkalis, and many organic solvents.
- Electrical insulation – excellent dielectric properties, suitable for cable sheathing.
- Fire retardancy – inherently flame-resistant, making it ideal for safety-critical applications.
- Rigidity or flexibility – available in rigid or plasticized grades depending on your needs.
Property | Density | Tensile Strength | Flexural Strength | Impact Strength (Unnotched) | Heat Deflection Temp (0.45 MPa) |
---|---|---|---|---|---|
Value/Description | 1.3 - 1.45g/cm³ | 35 - 60 MPa | 45 - 85 MPa | 2-15 kJ/m² | 60 - 95℃ |
- The above parameters represent the baseline performance of the materials. Actual application should be dynamically optimized based on specific working conditions.
Looking for High-Quality PVC Injection Molding?
Advantages & Disadvantages of PVC Injection Moulding
PVC injection moulding is widely used in various manufacturing applications. Like any material, it offers both strengths and limitations. Understanding these trade-offs can help you choose the right injection molding solution for your PVC product and performance goals.
Advantages
- Excellent chemical and flame resistance – ideal for electrical and industrial applications.
- Cost-effective for high-volume production – suitable for custom PVC molding with complex geometries.
- Dimensional stability – low shrinkage rates result in precise parts.
- Flexible or rigid options – adapts to different mechanical and environmental needs.
Disadvantages
- Thermal sensitivity – degrades if overheated, releasing harmful fumes.
- Processing complexity – requires corrosion-resistant molds and precise temperature control.
- Lower impact resistance – rigid PVC may be brittle under high-impact loads.
- Bonding difficulty – limited adhesion without surface treatment or primers.
Applications of Injection Molding PVC
With its high-performance properties, injection molded PVC is used in a wide range of products. Our custom PVC molding services ensure quality, safety, and durability for various sectors:
Electrical & Electronics

- Cable insulation and connectors
- Enclosures and switches
- Circuit board carriers
Construction & Infrastructure

- Pipe fittings and drainage components
- Window profiles and wall panels
- Flooring trims and corner guards
Medical Devices

- IV components and fluid containers
- Tubing and connectors
- Disposable medical housings
Consumer Goods
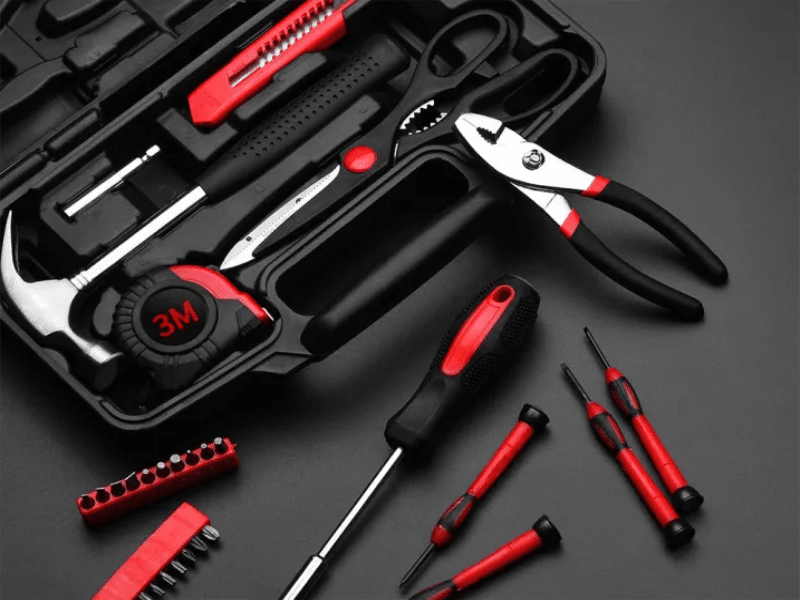
- Toys and flexible parts
- Decorative PVC mouldings
- Household tool handles and cases
Jiangzhi PVC Moulding Solutions are Guaranteed
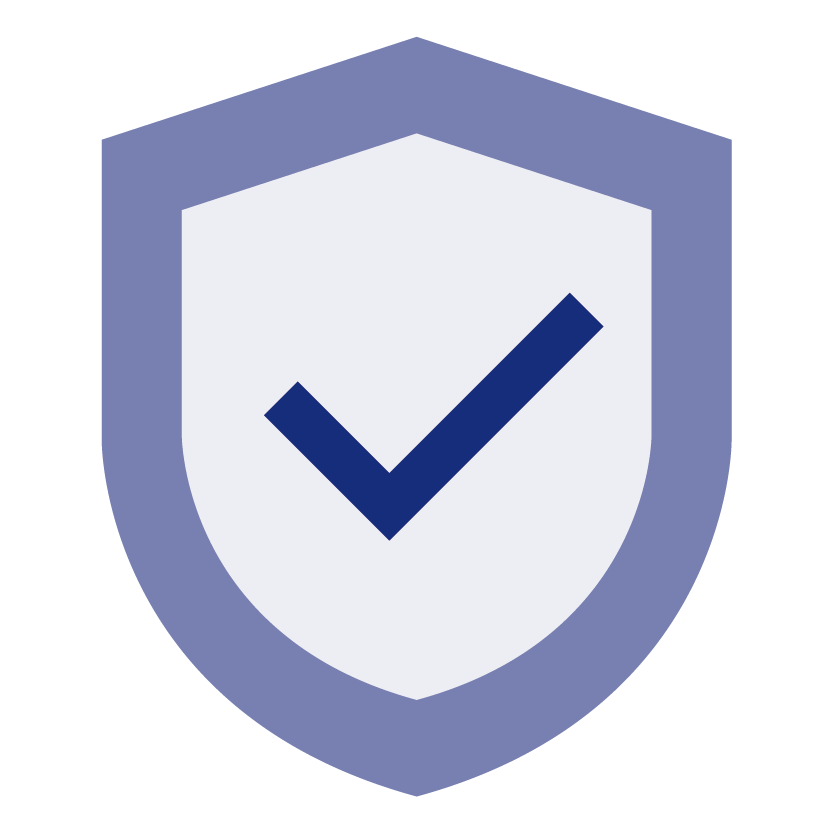