Design for Manufacturability
- Quality Manufacturing Starts with Good Design
- Decrease Tooling Rework, Reduce Cost
- Avoid 50% Injection Molding Defects
- Contract Manufacturer Engineering Service

A Well-Executed Injection Molding DFM Report Helps You
Confirms the feasibility of the product design for manufacturing
Optimizes the mold design plan for quality and cost-efficiency
Shortens the product development cycle by identifying issues early
Enhances collaboration between design and production teams
What Design for Manufacturability Can Tell You
We make DFM report to ensure the product design is suitable for manufacturing and to identify potential issues or areas for improvement before production begins. Following shows a simple design as an example, you will get to know that information you can get from a DFM report.
1. General Description

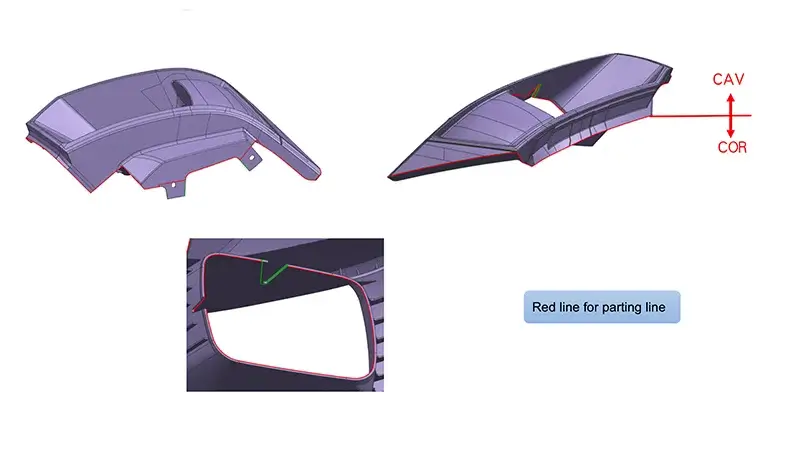
2. Parting Lines
Examines the location of the parting line (where the two halves of the mold meet).
Parting lines are usually located on the edges of the molded parts. However some lines may located around the middle of the part due to geometry structure.3. Gate Locations
Evaluates the optimal locations for gates (inlets for injecting molten plastic into the mold cavity).
The injection molding gate in the DFM report isn't the only option. You can inform us if it affects cosmetics or functionality. The gate type determines the way to produce and even the mass production cost.
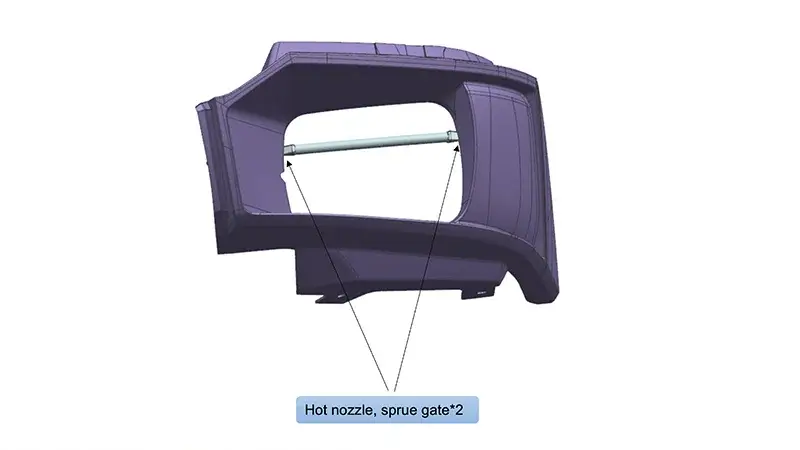

4. Lifters and Sliders
Assesses the need for and placement of lifters (movable mold components) and sliders (side-action components).
Lifter and silder are injection mold components to create undercuts.
5. Ejector Pin Marks
Analyzes the placement of ejector pins used to remove the molded part from the mold.
The ejector marks can not be removed due to the process of injection molding.


6. Rib and Wall thickness
Checks for uniform wall and rib thicknesses to prevent warping or other defects.
The thickness of the ribs should be about 60% of the wall thickness, avoid uneven wall thickness, avoid thin wall area as much as possible.7. Draft Angle
Evaluates draft angles (tapers) to ensure injection molded part easy release from mold cavity.
Sometimes it will slightly change the design of the original product.
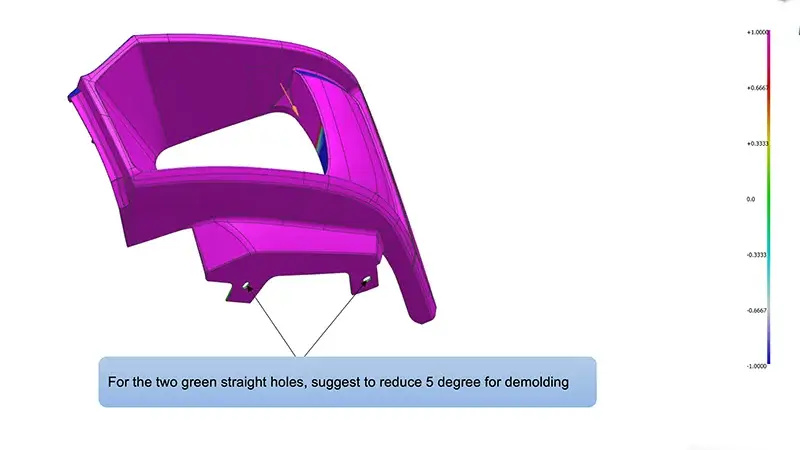

8. Problems & Solutions
9. Surface Finish Requirements
Specifications for the desired surface finish, which can have multiple finishes on a single part. Also define if there is any engraving or raised areas.
Normally we suggest determine texture or polish surface before machining the molds as the draft may not machined again as specified texture.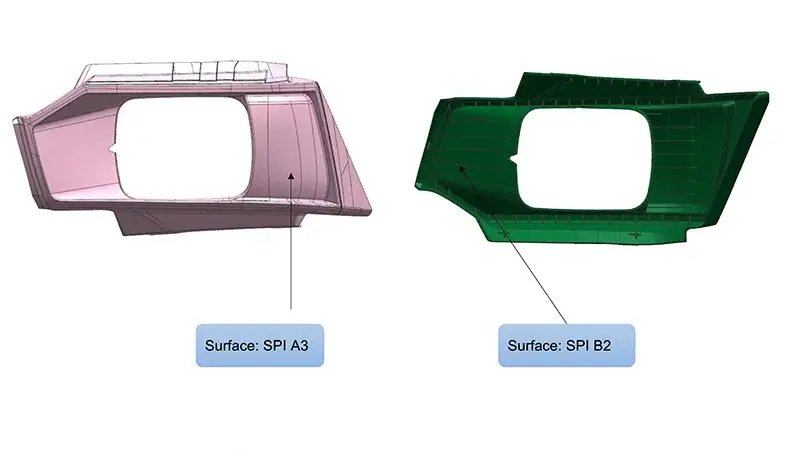
Upload Your CAD Files – Receive A DFM Analysis
FAQs About DFM Injection Molding
Mold Flow Analysis is a simulation that shows how plastic will flow inside the mold. It helps me spot issues like warping, sink marks, short shots, or weld lines before production. Including it in a DFM report helps avoid defects and costly mold changes later.
Usually 1–3 days, depending on the complexity of your part.
Yes, that’s the best time to make changes—before the mold is made.
No, it actually helps me save by preventing costly rework or delays.
Even simple parts can have issues. I prefer to catch them early rather than fix them later.
Jiangzhi Contact Manufacturer Capabilities
- Custom Automation Solutions
- Medium/High Volume Production
- Finished Retail Packaging