Injection Molding Tooling Service
-
- In-house mold fabrication service
- Injection molding tool design for manufacturability
- Maximum processing size: 2500mm×2000mm
- Tight tolerance up to ±0.02mm
- Lifetime mold guaranteed
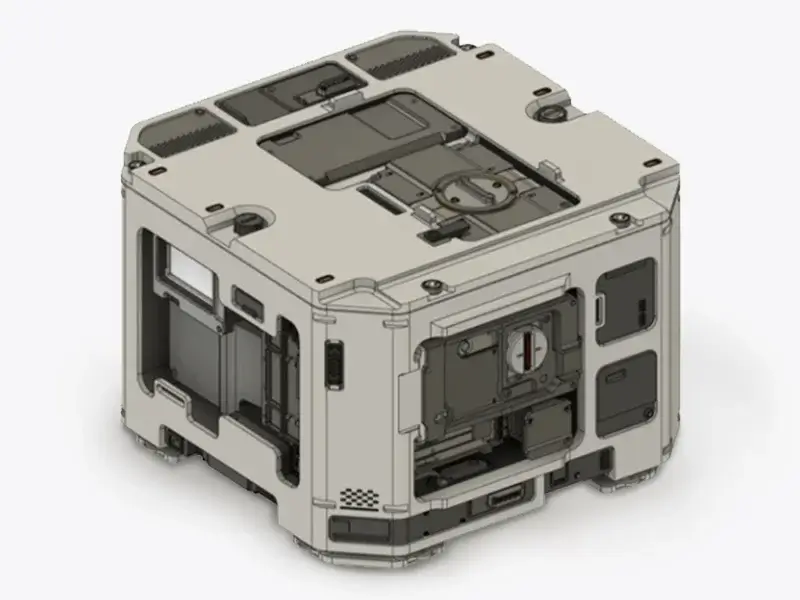



Mold Design for Complex Parts
We design and manufacture custom injection molds in-house, ensuring every tool is tailored to your part’s geometry and production requirements. Our skilled engineers and mold makers specialize in handling complex shapes, tight tolerances, and fine details—backed by advanced equipment and deep hands-on experience to get it right from the start. When it comes to complex mold design—like those with multi-cavity layouts, undercuts, inserts, or moving components—we take extra care to validate every detail. From DFM analysis to mold flow simulation and in-house trial runs, we ensure the tooling is production-ready before it hits the floor. Our rapid tooling service further accelerates the process, allowing you to get functional prototypes and bridge production tools quickly without compromising quality. This attention to detail helps avoid costly revisions and keeps your project on track.Injection Molding Tooling Capabilities
In injection molding, the core and cavity are pivotal structures that define part precision: the cavity shapes a component’s external contour, while the core forms its internal features. Their precise alignment underpins diverse injection mold designs—from single-cavity molds for custom parts to multi-cavity molds for mass production, and from hot runner systems enabling rapid filling to cold runner molds optimizing cost efficiency. Together, they ensure high-quality replication of complex geometries across all applications.
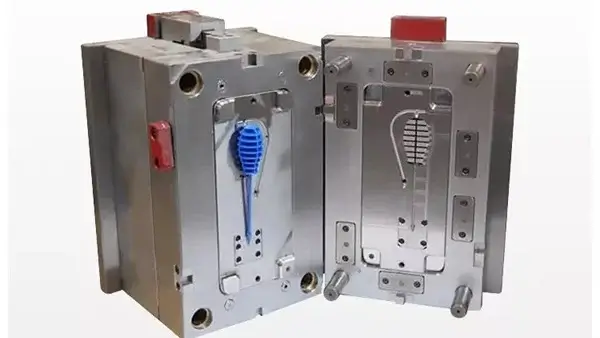
Single Cavity Mold
A single cavity mold is a molding tool designed for the production of individual components. This specialized mold ensures precise replication of specific parts, offering a tailored solution for projects with distinct requirements.
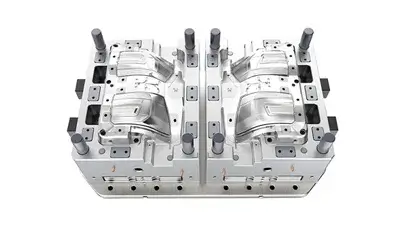
Multi Cavity Mold
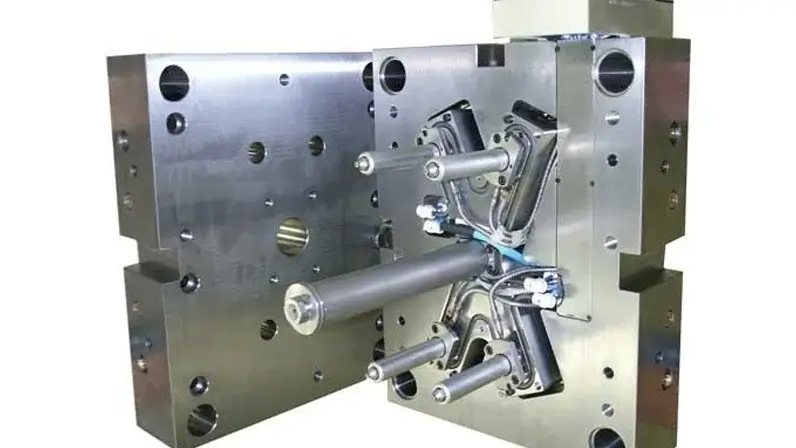
Hot Runner Mold
Advanced injection molding tooling featuring a heated manifold system. This innovative design ensures molten plastic is maintained in the runner system, reducing cycle times, minimizing waste, and delivering high-precision, consistent results.
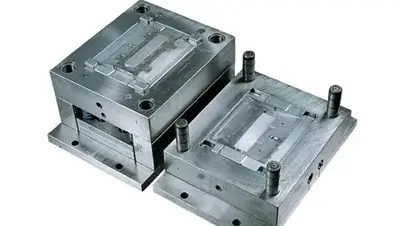
Cold Runner Mold
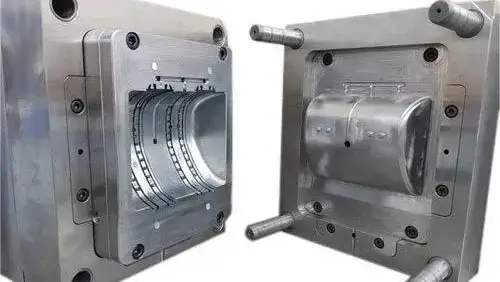
Two Plate Mold
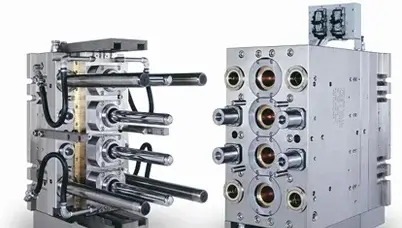
Three Plate Mold
Protect Your Custom Mold Tooling Investment
Your custom mold tooling is the foundation of efficient, high-quality production. Choosing the right plastic injection mold tooling service and maintaining your tooling for injection molding helps extend tool life, reduce costs, and ensure consistent part performance.
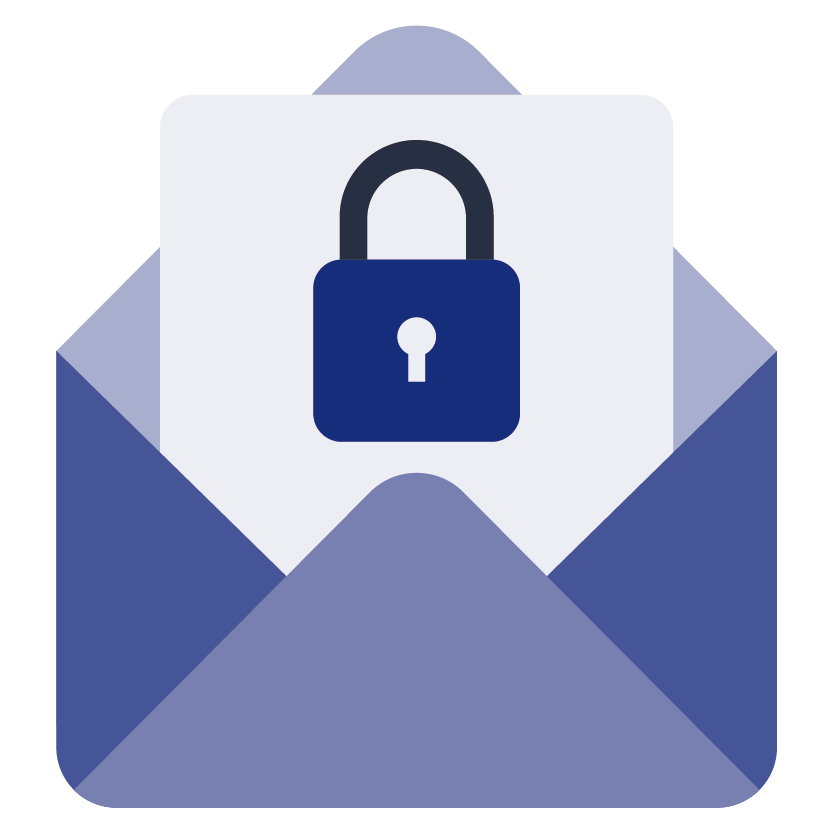
Confidentiality
Protecting your injection mold investment begins with stringent confidentiality measures. Our commitment ensures that your injection custom mold tooling design, specifications, and any proprietary infor mation remain strictly confidential. Entrust your project to us, where confidentiality is a cornerstone of our professional integrity.
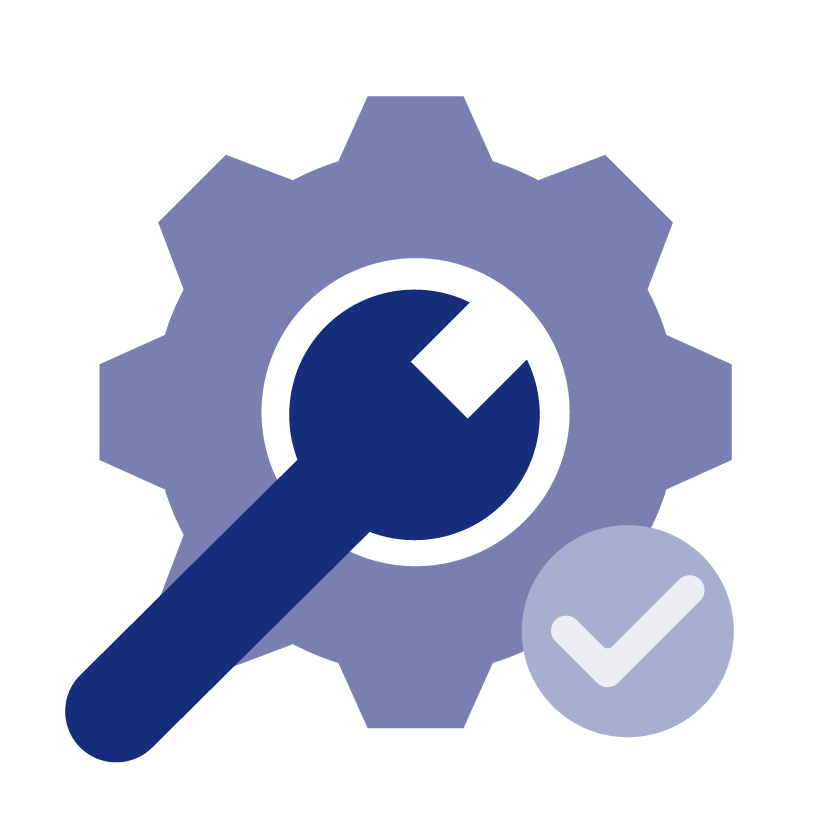
Maintenance
Considering potential repair costs, regular maintenance is vital for custom injection molds, safeguarding your investment and ensuring a consistent production of quality plastic components. Rely on our on-site tooling facility for efficient and timely mold repairs or revisions.
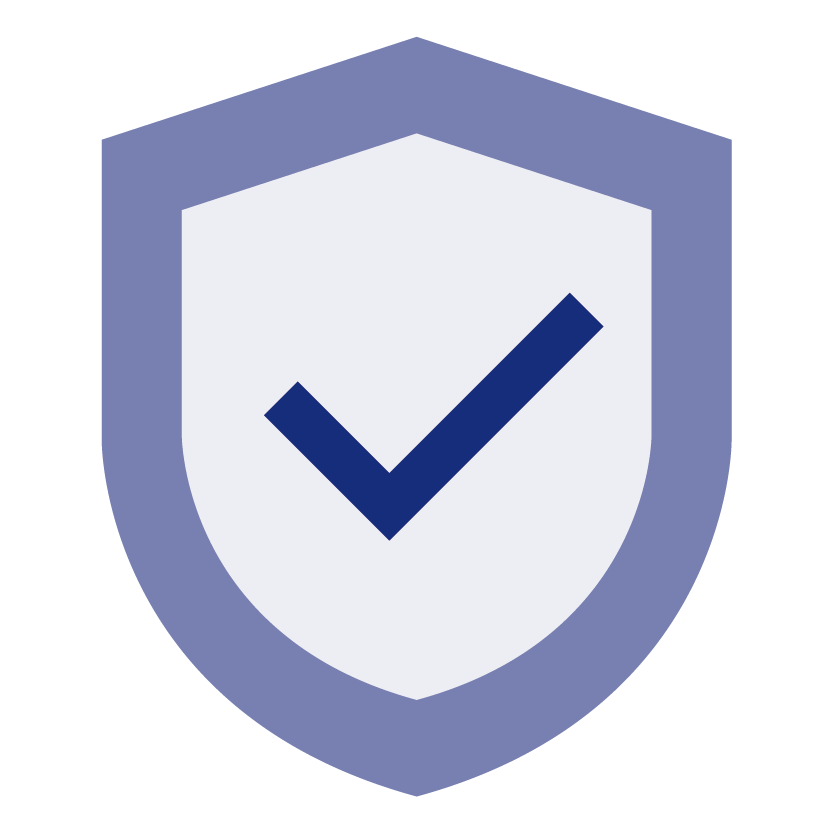
Lifetime guaranteed
Injection molds commonly withstand millions of shots before wear, and if wear occurs, we'll replace the mold at our cost. Once your initial investment is made, you enjoy a lifetime guarantee—use it forever without additional expenses. This commitment reflects our dedication to enduring quality.
Plastic Injection Mold Tooling Materials
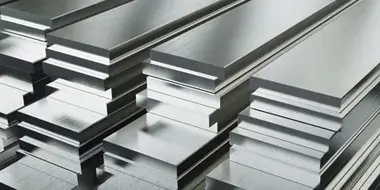
Tool Steel
- P20
- H13
- S7
- NAK80
- S316
- S316H
- 718
- 718H
- 738
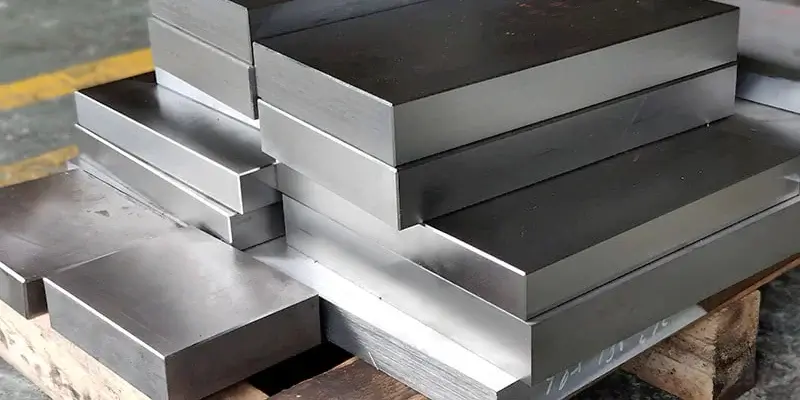
Stainless Steel
Custom injection molds, often made from pricey steel and stainless steel, are reserved for large-scale production due to their durability and precision.
- 420
- NAK80
- S136
- 316L
- 316
- 301
- 303
- 304

Aluminum
- 6061
- 5052
- 7075
Mold & Tooling Production Process
1. Custom Mold Tooling Design
b. 2D/3D modeling mold design;
c. CNC programing design.
2. Mold Material Procurement
3. CNC Machining the Mold
4. Electrical Discharge Machining
5. Polishing and Assembly
Some precision grinding is done on the plastic injection mold tooling components to ensure meet tight tolerances, and then mold the right finish. Finally assemble the mold components together correctly.
6. Samples and Necessary Improvement
Jiangzhi Contract Manufacturing Service
Producing high-quality plastic and rubber parts requires more than just great injection molding tooling design. Jiangzhi help you manage fast-changing production needs with full injection molding solutions—built for speed, flexibility, and cost-efficiency.
Mold & Tooling Related FAQs
How long does it take to make an injection mold?
In general, a simple mold can be completed in 4-6 weeks, while a complex mold might take 6-8 weeks. Aluminum molds, often used for prototypes, can be produced in 2-3 weeks
How many times can you use an plastic injection mold?
A plastic injection mold lifespan depends on its environment, maintenance, structure, SPI classification, and other factors. Generally, plastic injection molds last from hundreds to over a million cycles.
Is custom injection molding tooling cheaper in China?
While many countries offer mold-making services, China injection mold companies are the primary player in this market. Your company might be leaning toward China because their plastic injection molding services are generally low-cost, you’ll likely save between 20-60% with an injection mold made in China. You may also achieve faster results.
What material is used for injection molding tools?
Injection mould tools can be manufactured in several different mateirals, the most common are P20, H13 steels and aluminum.
Popular Post
Tap into industry-leading knowledge—whenever you need it. Our Resource Center is your go-to hub for everything related to injection molding tooling services and molding solutions. It offers a rich collection of informative articles, real-world case studies, and step-by-step guides to help you better understand and apply complex manufacturing processes.