Polytetrafluoroethylene, commonly known as PTFE or Teflon, is a fluoropolymers, celebrated for its chemical resistance, thermal stability, low friction, and thermal resilience. However, when it comes to manufacturing, especially via injection moulding PTFE, the material presents unique challenges that set it apart from conventional thermoplastics. This article explores the complexities of injection molding PTFE service, the reasons behind these difficulties, alternative processing methods, and practical design and material selection tips to optimize PTFE part production.
What is PTFE?
PTFE is a polymer composed of repeating units of tetrafluoroethylene, with a chemical structure represented as —(CF₂—CF₂)n—. The strong carbon-fluorine bonds confer remarkable chemical inertness and thermal stability, allowing PTFE to withstand temperatures from -180°C up to approximately 260°C without degradation. The friction coefficient as low as 0.05-0.10, resistance to nearly all chemicals.
Compared to other fluoropolymers such as PFA (perfluoroalkoxy alkane) and FEP (fluorinated ethylene propylene), PTFE boasts non-stick surface extremely low coefficient of friction, excellent electrical insulation, and resistance to UV and weathering. However, unlike PFA and FEP, which are melt-processable and compatible with conventional injection molding, PTFE’s unique molecular structure leads to a gel-like melt state rather than a true fluid melt, complicating injection molding processes.
Why PTFE Resists Traditional Injection Molding?
The primary hurdles in injection moulding PTFE stem from its high melt viscosity, thermal sensitivity, and processing characteristics that differ fundamentally from typical thermoplastics:
High Melt Viscosity: PTFE does not melt into a fluid state but transitions into a highly viscous gel-like phase near its melting point (~327°C). Its viscosity, often exceeding 10^10 Pa·s. This extreme viscosity prevents the polymer from flowing easily through injection molding equipment and mold cavities, making traditional injection molding virtually impossible.
Thermal Decomposition Risks: Heating PTFE above 350°C triggers decomposition, releasing toxic gases like hydrogen fluoride. The degradation temperature is close to its melting point. This necessitates robust ventilation systems and precise temperature control during Teflon injection molding.
Sintering Requirement: Unlike most plastics, PTFE requires post-molding sintering at 360-380°C to fuse its crystalline particles into a cohesive part. This additional step complicates the PTFE injection moulding process.
Demolding Challenges: PTFE’s non-stick nature, while a boon for applications, hinders demolding. Its high thermal expansion (2-5% shrinkage) can lead to warping or cracking if molds lack proper release mechanisms.
Mold Contamination: PTFE’s reactivity with certain mold materials accelerates wear, necessitating non-stick coatings or frequent mold maintenance to sustain injection molding PTFE operations.
Can PTFE Be Injection Molded?
Conventional injection molding of pure PTFE is not feasible due to the reasons above. The material’s gel-like melt and sintering requirements mean it cannot be processed like typical thermoplastics.
Advances in materials science have led to modified PTFE compounds that incorporate fillers such as glass fibers, carbon, or graphite to improve flow characteristics and mechanical properties. These modified PTFE compounds retain core properties like chemical resistance while enabling PTFE injection moulding.
However, some assume PTFE can be processed like standard thermoplastics, overlooking the need for high-pressure systems and sintering. Others believe fillers drastically compromise PTFE’s benefits, when in fact, additives like glass (up to 25%) can boost strength without sacrificing chemical inertness.
The PTFE Injection Molding Process: A Step-by-Step Overview
Mastering PTFE injection moulding requires a tailored process that accounts for the material’s unique behavior.
Material Preparation: PTFE powder is mixed with processing aids, such as PFA or lubricants, to improve flow.
Heating and Injection: The mixture is heated in high-temperature barrels (around 327°C) and injected into molds using specialized high-pressure systems (often exceeding 10,000 psi). Specialized non-stick coatings on molds prevent adhesion.
Debinding: Post-injection, parts undergo debinding to remove processing aids, ensuring purity before sintering.
Sintering: Parts are heated to 360-380°C in a controlled oven to fuse PTFE particles, forming a solid, durable structure.
Post-Processing: Machining or finishing may be necessary to achieve precise dimensions or surface quality due to shrinkage and warping during sintering.
Alternative Manufacturing Processes for PTFE
When PTFE injection moulding is not feasible, alternative manufacturing methods provide effective solutions for shaping PTFE, each tailored to specific part geometries and production needs.
Compression Molding
Ideal for simple shapes like sheets, gaskets, and seals, this process compacts PTFE powder under 3,000–10,000 psi, followed by sintering at 360–380°C. It’s cost-effective for low- to medium-volume production but limited for complex shapes due to mold constraints.
Extrusion Molding (Ram/Paste Extrusion)
Used for creating continuous PTFE shapes, shuch as tubes, rods, and profiles, ram extrusion pushes granular PTFE through a die, while paste extrusion uses a lubricated PTFE paste, sintered at 360–380°C. Extrusion is highly efficient for high-volume production of consistent profiles but is limited to linear or simple cross-sectional shapes, making it unsuitable for complex or custom geometries.
CNC Machining
Starting with pre-formed PTFE stock (often produced via compression or extrusion), PTFE CNC machining crafts precise parts with tolerances as low as ±0.01 mm. Ideal for prototypes, small-batch production and complex geometries, it generates more material waste and is costlier for large runs.
Typical Applications of Injection Molded PTFE Parts
Despite processing challenges, injection molding PTFE or its modified variants is used in applications demanding the material’s unique properties.
- Sealing Components: O-rings, gaskets, and valve seats for chemical processing equipment.
- Electrical Insulators: High-performance insulators and connectors in electronics and aerospace.
- Medical Devices: Catheters, seals, and implant components benefiting from PTFE’s biocompatibility and chemical resistance.
- Chemical Industry Parts: Liners, bushings, and pump components exposed to aggressive chemicals.
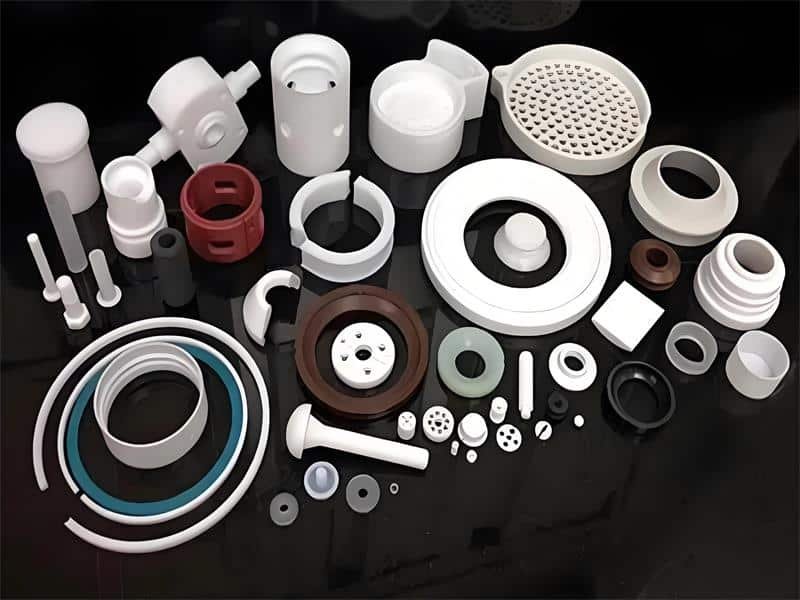
Design Suggestion and Material Selection Tips
To optimize injection molding PTFE parts, designers and engineers should consider:
Wall Thickness: Maintain uniform and sufficient wall thickness (generally ≥3 mm) to ensure consistent sintering and reduce warping.
Draft Angles and Demolding: Incorporate adequate draft angles (typically 1°–3°) to facilitate demolding and minimize surface defects.
Venting Structures: Incorporate vents in molds to release gases during molding, reducing defects like voids or burns.
Shrinkage Allowance: Account for unpredictable shrinkage during sintering by oversizing parts or planning for post-machining.
Process Control: Collaborate closely with manufacturers to define precise temperature profiles, injection pressures, and sintering cycles tailored to the part design and material grade.
Material Choice: For injection molding, prefer modified PTFE compounds with fillers that improve flow and mechanical properties. Alternatively, consider PFA or FEP if injection molding pure PTFE is infeasible.
Conclusion
Injection molding PTFE is a challenging process. Understanding the unique processing requirements, including high melt viscosity, sintering needs, and demolding challenges, will help to make the PTFE injection molding success. Jiangzhi, a professional manufacturer, supply expert PTFE injection molding service, delivering tailored solutions for various industries products requirements.