Rubber molded tolerance, as the name suggests, is the tolerance an industrial rubber product has according to its variable size.
Rubber molding tolerance figures are based on plus or minus (±) values that depict different part sizes. You may have seen several dimensions in engineering drawings, but remember that rubber and metal part tolerances are different. Hence, if you change your material midway, you may have to redesign everything.
The RMA Handbook is an excellent way of staying on track and avoiding mistakes. From standards to design requirements, this book gives you the necessary information regarding molded or extruded rubber products. But if you have any queries, continue reading!
What is Compression Molding?
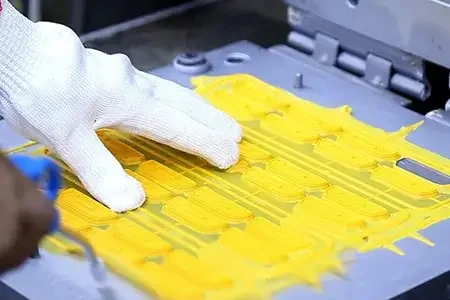
Compression molding is done with heat and pressure. A piece of rubber material is placed in a heated mold, and a controlled amount of pressure and heat is applied until the rubber is cured. The process requires a lot of time so that the rubber can properly harden and take up the shape of the mold.
To finalize the process, a mold containing both male and female components is used to seal the shape of the rubber. It helps exclude the extra material so that you get fine edges.
Why Should You Know Rubber Molding Tolerances?
Many engineers memorize metal part tolerances and apply the same values to rubber. However, it is hazardous in the case of rubber seals, gaskets, or insulation. Since both materials have different properties, you must always consider molded rubber tolerances. Rubber molding is often deemed the same as metal fabrication, but both methods differ a lot.
Fixed and Closed Tolerance
Fixed Dimension
In this tolerance, the entire insides of the steel cavities are machined. When the raw material is compressed, rubber is evenly pushed into all the holes to achieve a definite shape.
But you must ensure that the mold dimensions are marked on a non-critical rubber part and that the parting line between the two molds doesn’t hinder the rubber.
Closed Dimension
Closed dimensions(also called closure dimensions), on the other hand, are the areas that change when the molds are closed. The rubber comes under immense pressure when the mold is closed, causing some material to leak. This extra rubber is known as a “flash” and should be trimmed away once the rubber has hardened.
Four Levels of Rubber Parts Tolerance
To get the values and dynamics right, you must understand all four levels of rubber tolerances.
- A1 (High Precision): A1 offers you the highest level of tightness but is very expensive. The equipment required to achieve this tolerance also doesn’t come cheap, but it will give you almost zero cavities. However, you will need more quality checks and inspections to satisfy clients.
- A2 (Precision): At this level, you will have a rubber product that is precisely molded and one that doesn’t require many repairs.
- A3 (Commercial): Vastly used, this tolerance level offers you satisfactory precision and is often present in A2 and A1 tolerances.
- A4 (Non-Critical): A4 tolerance is commonly used where there’s little control over dimensions.
A1 and A2 tolerances often are the first choice for designers. However, they’re not cost-effective and also not suitable for all rubber parts. Therefore, knowing the dynamics of all the tolerances becomes extremely important so you can make the correct choice.
Rubber Tolerances Standard Chart
Table 1: A1 – High Precision
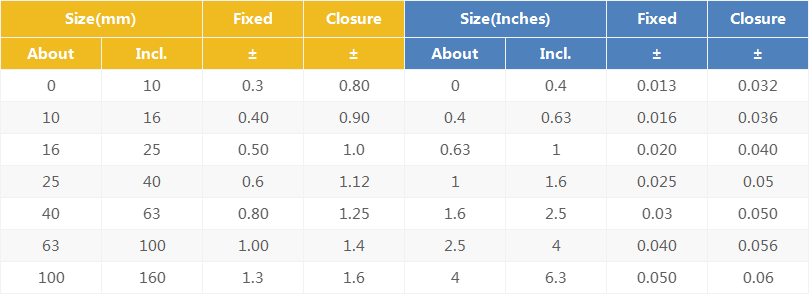
Table 2: Precision A2
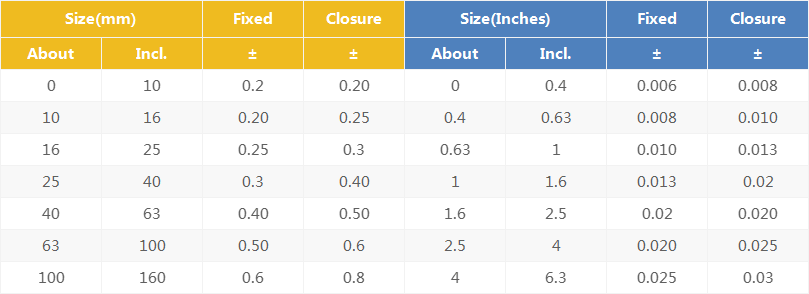
Table 3: Commercial A3
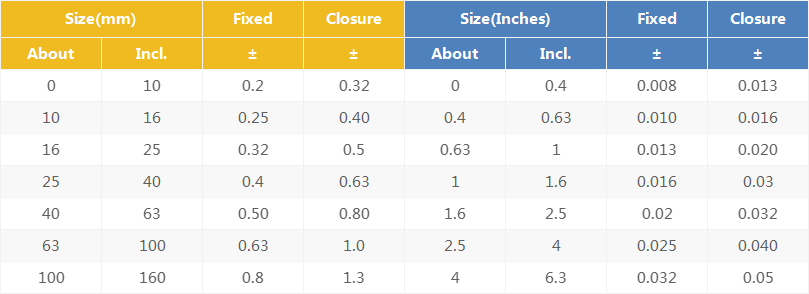
Table 4: Non-Critical A4
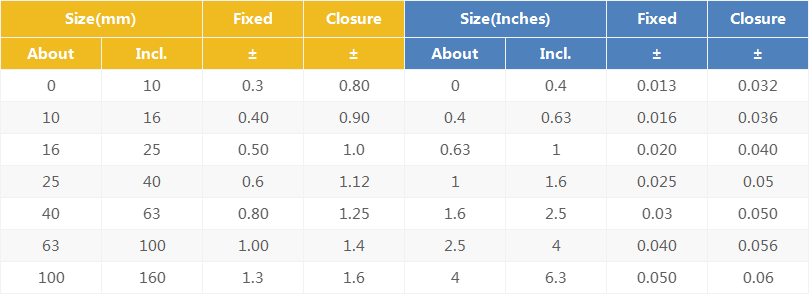
Factors That Affect Tolerance
Several factors affect a rubber product’s tolerance.
Mold Design
The design’s complexity directly affects the cost. The number of variations and cavities also impacts the mold design.
Shrinkage
Rubber shrinks considerably after cooling, so you need to be flexible with dimensions. Softer rubbers will shrink more than firm ones, so keep enough room to bear the shrinkage.
Trim & Finishing
Once done with molding a rubber product, you’d have to trim all the excess ends to give it a smooth look. It doesn’t usually affect the dimensions, but be careful if you have an intricate design.
Environmental Storage Conditions
Finally, environmental conditions affect rubber products even after completion. Make sure you provide adequate temperature settings for all your rubber products.
Applying Dimensional Tolerances
You may determine the tolerance accurately, but its application differs in every case. Therefore, you should consider these parameters before applying a tolerance:
- Calculate all the fixed dimensions individually, depending on their size.
- Fixed and closed dimensions aren’t co-related in all places.
- Determine closure dimensions by the largest closure, then you’ll be able to use this single tolerance for all the other closure dimensions.
- Use cavity segments to run capability studies. This will help you assign individual tolerances.
That’s about it! Hopefully, this brief overview of rubber molding tolerance is useful!