Modern-day manufacturers use various tools and methods to measure a material’s resistance. If you’re part of the engineering and manufacturing world, you understand shore rubber hardness inside and out. Without getting too technical – see hardness as a material’s resistance to deformation in the form of indentation. And this rubber resistance can be from scratching, cutting, or bending.
Technically, deformation comes into play when there is a consistent compression loan. On this topic, there is a wide range of tests to measure the key dimensions. What’s interesting is that you can run various hardness tests to determine a harness value for a similar material.
For instance, Shore A measurement hardness stems from a standard shore durometer tool. You can use this tool to measure the actual rubber elastomers and polymers hardness. The measured value shows the resistance to potential indentation. If the scale number is higher, there is bound to be more hardness. On the other hand, the lower number represents softer materials.
Let’s dive into the basics of rubber hardness, rubber testing methods, comparison scales, rubber hardness applications, and rubber hardness ranges.
The scaling of the rubber harness comes from Albert Ferdinand Shore, responsible for defining the rubber hardness scale and developing the standard shore durometer for measurement.
In layman’s terms, shore hardness indicates the measure of a specific material’s overall resistance to indentation or penetration.
When it comes to rubber, you measure the hardness of the surface using a traditional Shore hardness durometer.
Importance of Rubber Hardness
In terms of design, rubber hardness is an essential component. It is an anti-vibration mount factor that renders a specific amount of isolation. Manufacturers focus on added flexibility and lean towards suitable rubber hardness for a specific application and component.
Engineers take many considerations when it comes to supporting the load and providing frequency for successful isolation. In a technical sense, isolation is the degree of vibration reduction passed across the oscillatory system.
Standard Rubber Testing Methods
You can use various testing methods to measure rubber hardness. Over time, ASTM has become the hallmark testing method. Understand that the rubber usually falls between the 20 to 90 Shore A range.
ASTM D-2240
This testing technique uses a dedicated tool that indents the rubber and concentrates the specified condition. And this makes it easier to measure the material indentation. You can use this method to measure the indentation of vulcanized rubber, gel materials, elastomeric materials, and thermoplastic elastomers.
What About IRTD?
IRHD, or International Rubber Hardness Degree, is a European rubber testing method to measure the indentation resistance of rubber or elastomeric materials. You can measure the indentation resistance of materials in different sizes and shapes.
When measuring rubber hardness, focus the outcome based on the penetration depth of the ball indentor. In some elastic materials, Shore A and IRHD are not so different. The IRHD test is non-destructive and has become a highly popular and faster approach to inspecting final products.
How to Measure Rubber Hardness?
You can measure Shore rubber hardness using an indentation device like a Shore durometer. Every shore durometer features a truncated cone indenter pressed on top of a rubber sample.
Check out our video here to learn how you can measure rubber hardness.
As a standard, you can measure the rubber hardness through a durometer gauge. Focus on the three essential types of hardness:
SHORE 00
It measures gels and rubbers with a high degree of soft touch, like gel inserts and gummy candies.
SHORE A
It is the most common scale category of hardness. This scale ultimately measures whether or not mold rubbers are flexible. In terms of range, Shore A uses extremely hard and soft rubber.
SHORE D
It measures hard rubbers and can measure extremely hard or moderate hardness. This scale caters to semi-rigid and hard plastics.
NOTE: In time, the resilience of plastics and rubbers shows indentation can change. It is the main reason indentation in the table below is reported side-by-side with the hardness figure.
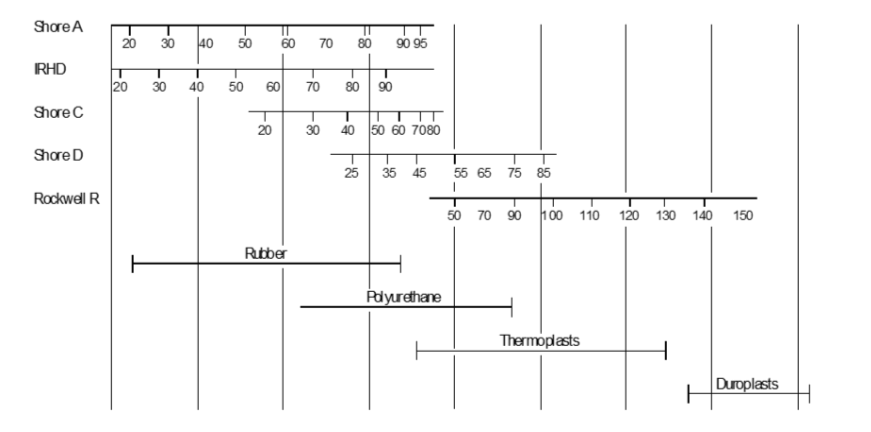
Shore Rubber Hardness Shore Examples and Applications
Each application requires a unique hardness level, ensuring successful sealing and much more. You can find one of the applications of rubber hardness in modern vehicles that use various Shore A rubbers.
For instance, soft to mid-range Shore A rubbers are used in gaskets, masking caps, seals, etc. However, hard (60+A) rubbers are used in grommets, o-rings, tire treads, rubber bushings, and panel plugs.
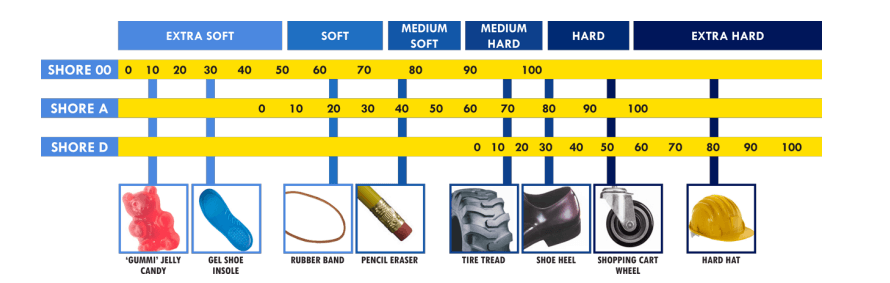
What Affects Rubber Hardness
Rubber hardness impacts the component’s stiffness. And this, in turn, affects the performance of a component in an application. For instance, human touch can separate the rubber hardness difference and isolation. Friction and texture also impact the hardness perception
Here’s to hoping you learned a thing or two about rubber hardness and shore durometer. Depending on the application and use case, the suitability of the test can differ. Once you move past the basics of shore rubber hardness, it becomes clear why it is important. If you’re getting ready to start selecting rubber, opt for the best quality rubber compound that can support multiple applications.