LDPE Injection Molding

What is LDPE Injection Molding?
Low-density polyethylene (LDPE) injection molding is an efficient manufacturing process used to produce lightweight, flexible, and chemically resistant plastic components. Our expertise in polyethylene injection molding ensures that every product meets high standards of durability, elasticity, and processability.
- Mold Design: Optimized to enhance flow properties and prevent shrinkage.
- Processing: LDPE injection molding involves melting the polymer at controlled temperatures and injecting
- Cooling & Solidification: Proper cooling ensures uniform thickness and prevents deformation.
- Post-Processing: Secondary treatments such as printing, heat sealing, and welding improve product performance.
With LDPE’s unique flexibility and impact resistance, we deliver cost-effective solutions across industries requiring lightweight and resilient plastic products—backed by expert DFM support, precision mold tooling services, high-quality surface finishing, efficient assembly manufacturing, and strict quality management.
LDPE Injection Molding Parameters
Parameter | Recommended Range |
---|---|
Wall Thickness | 0.5mm - 5.0mm |
Maximum Part Size | 1200mm x 800mm x 500mm |
Minimum Feature Size | 0.3mm - 1.5mm |
Tolerances | ±0.05mm - ±0.20mm |
LDPE Material Properties
LDPE injection molding is widely used for flexible and impact-resistant applications. Its low density, moisture resistance, and good processability make it ideal for packaging, medical, and industrial products. Key Material Properties:
- High Flexibility – Ideal for soft, bendable components.
- Excellent Chemical Resistance – Resistant to acids, alcohols, and dilute alkalis.
- Moisture & UV Resistance – Performs well in outdoor and humid environments.
- Lightweight & Durable – Low-density material with superior toughness.
Property | Density | Tensile Strength | Flexural Strength | Impact Strength (Unnotched) | Heat Deflection Temp (0.45 MPa) |
---|---|---|---|---|---|
Value/Description | 0.91 - 0.94g/cm³ | 8 - 15 MPa | 20 - 25 MPa | >10 kJ/m² | 40 - 60℃ |
- The above parameters represent the baseline performance of the materials. Actual application should be dynamically optimized based on specific working conditions.
Looking for Reliable LDPE Injection Molding?
Advantages & Disadvantages of LDPE Injection Molding
LDPE injection moulding is a commonly used method across various industries—but like any material choice, it comes with trade-offs. Knowing the ldpe Injeciton molding service pros and cons can help you make smarter design and manufacturing decisions.
Advantages
- Superior Flexibility – Ideal for soft, bendable, and squeezable products.
- Excellent Chemical Resistance – Suitable for packaging and medical applications.
- Moisture & UV Resistance – Performs well in humid and outdoor environments.
- Lightweight & Recyclable – Cost-effective and eco-friendly.
Disadvantages
- Lower Heat Resistance – Softens at temperatures above 60℃.
- Limited Rigidity – Not suitable for high-load applications.
- Difficult to Bond – Poor adhesion to paints and coatings.
Applications of LDPE Injection Moulding
Industrial & Packaging

- Flexible tubing & pipes
- Protective packaging films
- Chemical-resistant containers
- Stretch wraps & shrink wraps
Medical & Healthcare
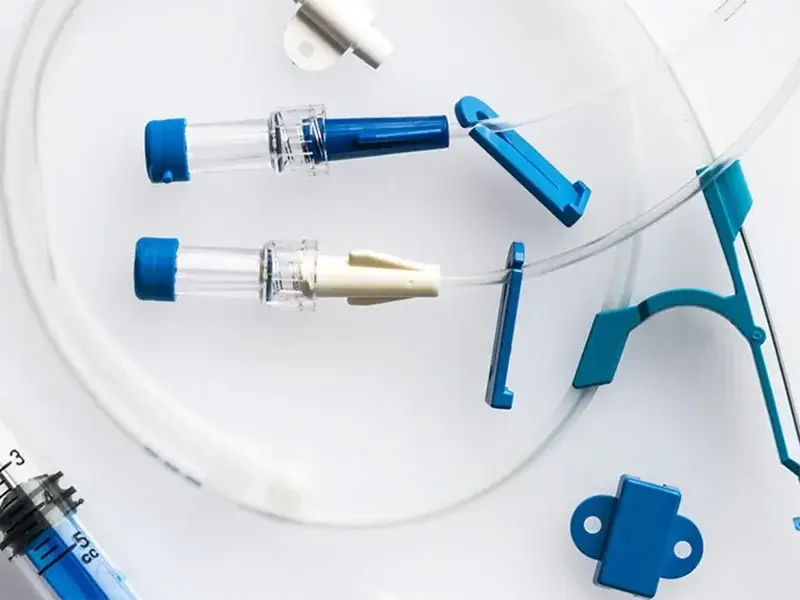
- Medical-grade tubing
- Sterile packaging materials
- Disposable syringes & gloves
- Flexible IV bags
Consumer & Household
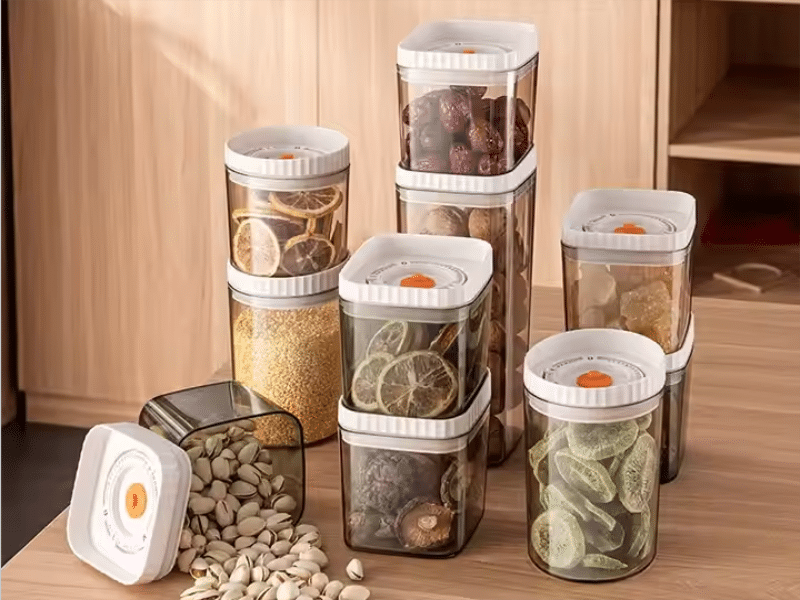
- Squeeze bottles & caps
- Soft-touch grips & handles
- Food storage containers
- Flexible lids & packaging films
Electronics & Electrical

- Wire and cable sheath
- Insulation film & electronic component packaging
- Flexible circuit board protective film
Jiangzhi LDPE Injection Molding Parts Are Guaranteed
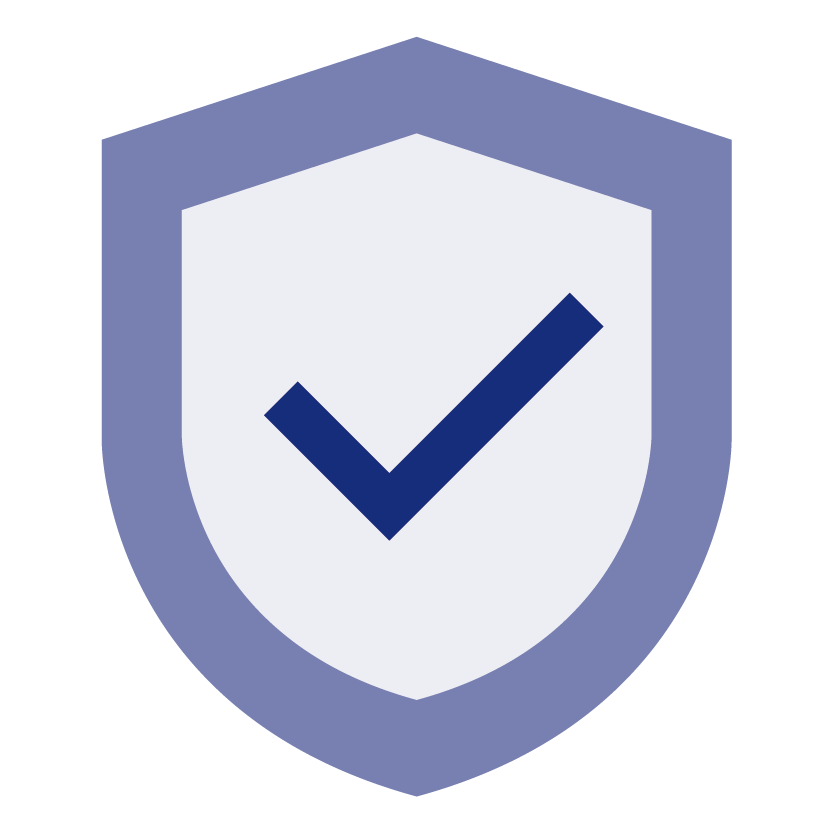
FAQs About Injection LDPE Molding
LDPE molding is more flexible and impact-resistant, while HDPE injection molding is stronger, more rigid, and has higher chemical resistance. The choice depends on the application needs.
LDPE has higher shrinkage rates and lower strength compared to other plastics, requiring precise mold design to ensure quality and dimensional accuracy.
LDPE works well with high-polish steel molds for smooth finishes and hot runner systems to minimize waste and improve efficiency.
Costs vary based on mold complexity, part size, production volume, and material grade. Low-volume runs may have higher per-unit costs, while high-volume production is more cost-effective.
Yes, LDPE is recyclable, and many manufacturers use recycled LDPE to reduce costs and environmental impact.