Molded part corner design plays a pivotal role in the overall performance and manufacturability of molded parts. Properly designed corners can significantly enhance the structural integrity, aesthetics, and functionality of a part. In contrast, poorly designed corners can lead to a range of issues such as increased stress concentration, material flow problems during molding, and higher production costs due to mold wear and part failure. In this post, we will explore plastic molded part corner design tips, and considerations to create more efficient, reliable, and aesthetically pleasing molded parts.

Significance of Proper Molded Part Corner Design
The significance of proper molded part corner design in injection molding cannot be overstated. Here are the key reasons why corner design is crucial:
Even Stress Distribution: Rounded corners help distribute stress more evenly throughout the part, reducing stress concentration that can lead to part failure or reduced durability. Sharp corners, on the other hand, create high levels of stress during the injection molding process, impacting the part’s performance.
Better Material Flow: Properly designed corners with appropriate radii facilitate better material flow during molding. This improved flow helps prevent issues such as incomplete filling, weld lines, or other defects that can compromise part quality.
Enhance Part Strength: Increasing the corner radius can significantly improve impact strength. For example, increasing the inside corner radius from 0.010 inch to 0.020 inch can notably enhance the part’s ability to withstand loads.
Easier Manufacturability: Rounded corners are easier to machine in steel molds compared to sharp corners. This can simplify mold fabrication and reduce manufacturing challenges.
More Smoothly Part Ejection: Well-designed corners make it easier to eject the part from the mold without causing damage or deformation. This is crucial for maintaining dimensional accuracy and surface finish.
Enhance Aesthetics: The aesthetic appeal and surface finish of a molded part are significantly influenced by its corner design. Sharp corners can lead to poor surface quality, with visible marks, flow lines, or defects that detract from the part’s appearance. Rounded or filleted corners, on the other hand, allow for smoother material flow during the molding process, resulting in a more polished and visually appealing surface.
Types of Corners in Molded Parts
There are several types of corners commonly found in injection molded parts. Here’s an overview of the main types:
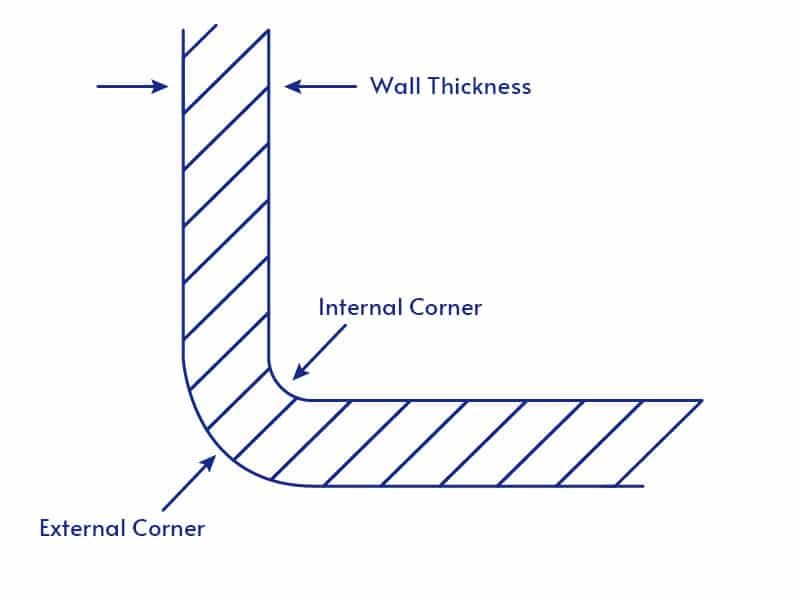
External Corners:
These are the outer corners of a part. They are typically designed with a radius to improve strength and manufacturability. The recommended radius usually ranges from 0.5 to 2 times the wall thickness.
Internal Corners:
These are the inside corners of a part. They are often designed with fillets to reduce stress concentration and improve material flow. The internal radius is typically smaller than the external radius to maintain uniform wall thickness.

Sharp Corners:
While generally avoided due to stress concentration issues, sharp corners are sometimes necessary, especially at parting lines. They can be challenging to manufacture and may require special considerations in mold design.
Rounded Corners:
These are corners with a significant radius, used to distribute stress, improve material flow, and enhance part strength. They are preferred in most injection molding designs.

Radiused Corners:
Similar to rounded corners, these have a specific radius applied to reduce stress concentration and improve moldability.
Filleted Corners:
These are internal corners with a concave radius transition, used to reduce stress concentration and improve material flow.
Chamfered Corners:
While not strictly a “rounded” corner, chamfers are sometimes used instead of radii, especially in parts where a specific edge profile is required.
Guidelines for Molded Part Corners Design
The general corner design principle is use rounded corners instead of sharp ones whenever possible. The recommended corner radii are related to different materials and the molded part’s wall thickness.
Recommended Radii for Different Materials
Thermoplastics: For most thermoplastics, a minimum radius of 0.5 to 1.0 times the wall thickness is recommended. This helps in reducing stress concentration and ensuring smooth material flow.
Thermosets: Thermosetting plastics, being more brittle, typically require larger radii. A minimum of 1.5 to 2.0 times the wall thickness is often suggested.
Elastomers: For elastomeric materials, which are more flexible, a minimum radius of 0.5 times the wall thickness is usually sufficient, though larger radii can further enhance durability and ease of molding.

Optimal Corner Radii Based on Part Thickness
Thin Walls: For parts with thin walls (less than 2 mm), a radius of 0.5 to 1.0 times the wall thickness is ideal. This ensures that the material can flow smoothly and the part retains sufficient strength.
Medium Walls: For medium wall thicknesses (2-4 mm), a radius of 1.0 to 1.5 times the wall thickness is recommended. This helps in distributing stress and maintaining structural integrity.
Thick Walls: For thick walls (greater than 4 mm), a radius of 1.5 to 2.0 times the wall thickness is typically required to manage stress and prevent defects like sink marks.
Why Avoid Sharp Corner on Molded Parts?
Sharp corners in injection molded parts present several significant challenges:
Stress Concentration Issues:
Sharp corners create areas of high stress concentration, which can lead to part failure or reduced durability. The stress concentration factor is particularly high when the radius-to-thickness (R/T) ratio is less than 0.5. This concentration of stress can significantly weaken the part, especially under load or impact.
Difficulties in Mold Filling:
Sharp corners impede the flow of molten plastic during the injection process. That will lead to incomplete filling of the mold cavity and short shots. Trapped air pockets will cause voids or surface defects. Local high temperatures may degrade the material. Injection pressure requirements will be increased.
Ejection Problems:
Parts with sharp corners are more likely to stick to the mold during ejection. This can cause damage to the part during removal. The cycle time will be increased due to difficult ejection. And the mold will easy to wear and tear.
Increased Risk of Part Failure:
The combination of stress concentration and potential molding defects significantly increases the risk of part failure. This is particularly true for materials sensitive to stress during molding, such as nylon and polycarbonate.
Reduced Impact Strength:
Sharp corners dramatically reduce a part’s ability to withstand impact loads. For example, increasing the inside corner radius from 0.010 inch to 0.020 inch can notably improve impact strength.
Mold Fabrication Challenges:
Creating sharp corners in molds, especially for internal features, can be difficult and may require specialized machining techniques like EDM (Electrical Discharge Machining). This increases mold complexity and cost.
Aesthetic Issues:
Sharp corners can lead to visible defects such as sink marks, flow lines, or inconsistent surface finish, affecting the part’s appearance.
How to Address Sharp Corner Challenges?
- Using rounded corners with appropriate radii (generally 0.5 to 2 times the wall thickness).
- Maintaining consistent wall thickness throughout the part.
- Implementing gradual transitions between different thicknesses when necessary.
- Considering material properties when determining corner design.
Why Are Rounded Corners Used in Design?
Studies have shown that increasing the inside corner radius from 0.010 inch to 0.020 inch can improve impact strength by up to 25% in some materials. The optimal corner radius is typically between 0.5 and 2 times the wall thickness, with the exact value depending on the specific material and application.
Rounded corners in injection molded parts offer numerous benefits that significantly improve both the manufacturing process and the quality of the final product. Let’s explore these benefits in detail:
Improved Stress Distribution:
Rounded corners distribute stress more evenly across the part, reducing stress concentration. This even distribution helps prevent localized weaknesses that could lead to part failure. The stress reduction factor can be significant; for example, a corner with a radius equal to the part thickness can reduce stress by up to 75% compared to a sharp corner.
Enhanced Mold Filling and Material Flow:
Rounded corners facilitate smoother material flow during the injection process. This improved flow results in more consistent filling of the mold cavity, Reduced risk of short shots or incomplete filling, lower injection pressures, which can extend mold life, and more uniform cooling leading to less warpage and better dimensional stability. Better flow also means fewer issues with weld lines, air traps, and other flow-related defects.
Easier Part Ejection:
Parts with rounded corners are less likely to stick in the mold during ejection. This leads to reduced cycle times, improved production efficiency, less damage to parts during ejection, decreased wear on mold components, extended mold life, and more consistent part quality across production runs.
Increased Part Strength and Durability:
Rounded corners significantly enhance the overall strength of the part. They improve impact resistance by distributing impact forces more evenly. This increased strength means higher load-bearing capacity, better fatigue resistance, improved long-term durability, and reduced likelihood of part failure in service.
Additional Benefits:
Improved Aesthetics: Rounded corners often provide a more polished, professional appearance.
Enhanced Safety: For consumer products, rounded corners reduce the risk of injury from sharp edges.
Better Mold Manufacturability: Rounded corners are easier to machine in mold steel, potentially reducing mold cost.
Material Savings: In some cases, the improved strength from rounded corners allows for thinner overall wall sections, reducing material usage.
Conclusion
Proper molded part corner design is a critical aspect of creating high-quality, durable, and manufacturable injection molded parts. By applying these best practices and considering the unique requirements of each project, designers and engineers can create parts that are not only visually appealing but also robust, efficient to manufacture, and well-suited to their intended function.
Essential Guidelines for Molded Part Corner Design
FAQs About Injection Molding Corner Design
The minimum recommended radius typically depends on the wall thickness, but general guidelines include: For external corners: Minimum radius of 0.5 times the adjacent wall thickness. For internal corners (fillets): Minimum radius of 0.5 times the adjacent wall thickness. A minimum radius of 0.010 inches (0.254mm) is often recommended to ensure dimensional stability.