The overmolding process is increasingly relevant in modern manufacturing due to its ability to combine multiple materials into one cohesive part. This not only simplifies the production process by reducing the need for secondary assembly but also enhances the performance characteristics of the final product. For instance, overmolding can improve grip and comfort in tools and consumer products, while also providing additional protection against environmental factors such as moisture and dust. In this post, we will explore overmoulding process, steps, design guide, materials, advantages, disadvantages and applications.Hope our overmoulding guide can help you.
What is Overmolding Process?
Overmolding is a multi-step injection molding process where two or more materials are molded together to create a single, integrated component. This process typically begins with the creation of a base component, known as the substrate, which is usually made from a rigid material such as plastic or metal. Following this, a second layer of material—often a softer thermoplastic elastomer—is injected over or around the substrate. This two-shot molding technique enhances the final product’s functionality, aesthetics, and durability, making it suitable for a wide range of applications, from consumer goods to industrial components.

Steps in the Overmolding Process and Considerations
The overmoulding process involves several critical steps that ensure the successful integration of different materials into a single part. Each step is essential for achieving the desired performance and aesthetic qualities of the final product.
Step 1: Material Selection
The first step in the overmolding process is selecting the appropriate materials for both the substrate and the overmold. Key criteria for material selection include:
Compatibility: The substrate and overmold materials must bond effectively during the molding process. This often involves choosing materials with similar thermal properties and chemical compatibility.
Mechanical Properties: Consideration of tensile strength, flexibility, and durability is crucial to ensure that the final product meets performance requirements.
Aesthetic Qualities: The color, texture, and finish of the overmold can significantly affect the product’s appearance, making it essential to choose materials that align with design goals.
Cost: Budget constraints may influence material choices, so balancing performance with cost-effectiveness is vital.
Step 2: Mold Design and Setup
Once materials are selected, the next step is mold design and setup. This phase involves several considerations:
Mold Construction: The mold must be designed to accommodate both the substrate and the overmold materials. Precision in mold design is critical to ensure proper fit and function.
Runner Design: The runner system must be optimized for efficient material flow during injection. This includes minimizing waste while ensuring uniform distribution of materials.
Gate Design: Gate placement affects how materials enter the mold cavity. Proper gate design can help prevent issues such as short shots or uneven fill, which are crucial for achieving high-quality overmolds.
Step 3: Injection and Cooling
In this step, the actual injection of materials takes place:
Injection Process: The substrate material is injected into the mold first, followed by the overmold material. Careful control of injection speed and pressure is necessary to ensure proper filling and bonding between layers.
Cooling Management: Cooling rates must be monitored closely to prevent warping or defects in the final part. Effective cooling strategies help maintain dimensional stability and enhance surface quality.
Step 4: Ejection and Inspection
After cooling, parts need to be ejected from the mold:
Part Ejection Methods: Various techniques can be used to eject parts from molds, including mechanical ejectors or pneumatic systems. The method chosen should minimize stress on the part to avoid damage.
Quality Control Checks: Inspecting parts for defects such as incomplete fills, surface imperfections, or bonding issues is essential.
Step 5: Post-Processing
The final step in the overmolding process involves additional finishing processes:
Finishing Processes: These may include trimming excess material, surface polishing, or applying coatings to enhance aesthetics and functionality. Post-processing can significantly improve product appeal and performance.
Overmolding Operations
Manual overmolding vs. 2-shot molding are two primarily overmolding operations.
Manual Overmolding
Manual overmolding is a straightforward and widely used technique, particularly for low to mid-volume production runs. In this method, the substrate is first created using a traditional injection molding process. Once the substrate is molded and cooled, it is manually placed into a second mold where the overmold material is injected. This hands-on approach allows operators to ensure that the substrate is positioned correctly before the overmolding occurs. The tooling required for manual overmolding is less complex compared to two-shot molding, making it easier to set up and operate.
Two-Shot Overmolding
Two-shot overmolding is an advanced injection overmolding techniques designed for high-volume production. This method involves a specialized injection molding machine equipped with multiple injection units. The first material is injected into the mold to form the substrate. Once solidified, the mold either rotates or shifts to allow for the injection of a second material directly onto the first layer. Automatic for 2-shot molding process enhances bonding between materials and reduces handling time.Two-shot molding achieves a strong bond between materials due to the simultaneous injection process, which allows for better molecular entanglement.

Overmolding Design Guidelines and Considerations
When designing for the overmolding process, several critical factors must be taken into account to ensure successful integration of materials and optimal performance of the final product.
1. Material Compatibility
The substrate and overmold materials must be compatible to ensure effective bonding. Typically, a rigid substrate is paired with a softer thermoplastic elastomer (TPE) for enhanced grip and comfort.
The melting temperature of the substrate should be higher than that of the overmold material to prevent deformation during the injection process.
2. Uniformity Wall Thickness
Maintaining uniform wall thickness between the substrate and overmold is crucial. A typical wall thickness of 1.5mm to 3mm is recommended to achieve good flow and bonding while minimizing cycle times.
Transitioning gradually between thick and thin sections can help improve material flow and reduce potential defects, such as back fills or gas traps.
3. Mold Design
Overmolding typically requires two overmolds—one for the substrate and another for the overmold. Thoughtful placement of gates and vents is essential for achieving uniform distribution of molten plastic and preventing air entrapment during injection.
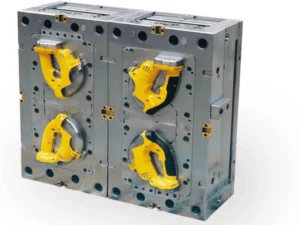
4. Adhesion Features
Incorporating undercuts or mechanical interlocks in the design can significantly enhance adhesion between the substrate and overmold, especially when chemical bonding is not feasible.
Texturing the surface of both the substrate and overmold can improve grip and increase surface area for better adhesion.
5. Cooling Considerations
Efficient cooling channels must be integrated into the mold design to maintain consistent cycle times and prevent defects like sink marks or warpage during cooling.
6. Ejection Mechanisms
The design should include effective ejection mechanisms, such as ejector pins, to facilitate smooth removal of parts from the mold without causing damage.
Enhance Your Products with Precision Overmolding!
Materials Used in Overmolding
The selection of appropriate materials is crucial in the overmolding process, as it directly impacts the performance, durability, and functionality of the final product.
Common Materials for Substrates
Substrates are the base materials onto which the overmold is applied. The most commonly used substrate materials include:
- Acrylonitrile Butadiene Styrene (ABS)
- Nylon
- Polycarbonate (PC)
- Polypropylene (PP)
Typical Overmold Materials
Overmold materials are typically softer plastics that provide functional benefits to the final product. Common overmold materials include:
- Thermoplastic Elastomers (TPE)
- Thermoplastic Polyurethane (TPU)
- Liquid Silicone Rubber (LSR)
Overmolding Advantages and Disadvantages
Advantages of Overmolding
The overmolding process offers numerous benefits that enhance product quality, functionality, and production efficiency. Below are some of the key advantages associated with overmolding:
Enhanced Product Functionality
One of the most significant advantages of overmoulding is the ability to improve product functionality. By combining different materials, manufacturers can create products with features such as soft-touch grips and improved ergonomics. For example, overmolded handles on tools and appliances provide a secure hold, reducing hand fatigue and increasing user satisfaction.
Cost-Effectiveness in Production
Overmolding can lead to substantial cost savings in the long run. Although the initial investment in molds may be higher, the reduction in labor costs and production time often outweighs these expenses. By creating a single integrated part instead of multiple components that require assembly, manufacturers can streamline their operations and reduce overall manufacturing costs.
Reduction in Assembly Time
By utilizing overmolding, manufacturers can eliminate extra assembly steps that would typically be required when using separate components. This integration results in a significant reduction in assembly time, leading to faster production cycles and lower labor costs.
Improved Durability
Overmoulding enhances the durability of products by combining materials with complementary properties. For instance, a rigid substrate can provide structural integrity while a softer outer layer offers impact resistance. This characteristic is vital in industries such as automotive and electronics, where products must withstand wear and tear. The combination of materials can also improve resistance to environmental factors like moisture and dust, further extending product lifespan.
Versatility in Applications
The versatility of overmolding allows it to be applied across various industries, from consumer electronics to medical devices. Manufacturers can tailor the process to meet specific requirements, such as improved grip or enhanced safety features.
Enhanced Aesthetics
Overmolding provides opportunities for creative design possibilities. Manufacturers can use different colors and textures to create visually appealing products that attract customers.
Customization Options
Another notable advantage of overmolding is the potential for customization. By using various materials and designs, manufacturers can create unique products tailored to specific customer needs. This ability to customize enhances customer satisfaction and loyalty, making overmoulding an attractive option for businesses aiming to meet diverse consumer demands.
Disadvantages of Overmolding
While the overmolding process offers numerous benefits, it also presents several challenges and limitations that manufacturers must consider.
Potential Challenges with Material Compatibility
One of the primary challenges in the overmolding process is ensuring material compatibility between the substrate and the overmold materials. Not all materials bond well together, which can lead to issues such as delamination or weak interfaces. For instance, if incompatible materials are used, it may result in inadequate bonding, causing the overmold to separate from the substrate under stress or during use . Manufacturers must conduct thorough compatibility testing to ensure that the selected materials will adhere properly during the overmoulding process. This includes evaluating chemical compatibility, mechanical bonding, and thermal properties to avoid potential failures.
Limitations in Design Complexity Due to Mold Constraints
Overmolding imposes certain design constraints that can limit creativity and complexity. The need for specialized molds and tooling can restrict the geometric freedom of parts. Complex shapes or intricate features may not be feasible due to the limitations of mold design and manufacturing processes . Additionally, consistent wall thickness is often required to ensure proper flow of materials during injection, which can further constrain design options. These limitations may necessitate compromises in product design, potentially impacting functionality and aesthetics.
Risk of Warpage or Defects if Not Properly Managed
The risk of warpage is a significant concern in overmolding, particularly due to differential shrinkage between the two materials during cooling. If not managed properly, this can lead to defects such as uneven surfaces or structural weaknesses in the final product . Factors contributing to warpage include variations in wall thickness, improper cooling rates, and inadequate mold design. Manufacturers must implement best practices for mold design and processing parameters to minimize these risks, such as optimizing cooling systems and ensuring uniform wall thickness throughout the part.
Applications of Overmolding Process
Overmoulding injection molding is a versatile manufacturing technique that finds applications across various industries due to its ability to enhance product functionality, aesthetics, and durability. Below are some examples of products that from over moulding
- Cable Overmolding
- Surgical Instruments
- Handheld Devices
- Consumer Electronics
- Kitchenware
- Hardware Tools
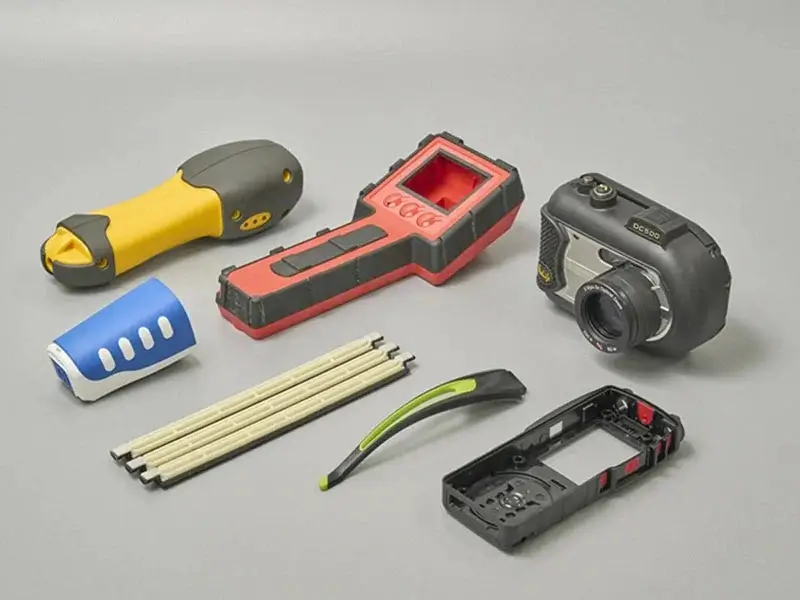
Conclusion
In summary, the overmolding process is a sophisticated technique that combines two or more materials to create a single, integrated component. This method enhances product functionality, aesthetics, and durability across various industries, including automotive, electronics, medical devices, and consumer goods. Jiangzhi is a professional manufacturer supply overmolding injection molding services. Welcome to contact if any overmoulding project requirements.