Compression moulding is a versatile manufacturing process widely adopted in industries such as automotive and aerospace. By applying heat and pressure, it produces high-strength, durable components—especially suited for medium to large injection parts like structural panels and consumer products. While its benefits are compelling, understanding its limitations is equally critical. This article explores the compression molding advantages and disadvantages, delving into its process, advantages of compression molding, and limitations.—highlighting not just the advantages, but also the trade-offs to consider when choosing this method over others.
What is Compression Moulding?
Compression moulding process transforms preheated materials—thermosets, thermoplastics, or composites—into solid parts by placing them in an open, heated mould cavity, compressing them under high pressure (500–4000 psi), and curing them. The process involves preheating materials like sheet moulding compound (SMC) or bulk moulding compound (BMC), loading them into a steel or aluminium mould, and applying heat and pressure to shape and cure the part. After cooling, the part is ejected. With cycle times of 1–10 minutes, compression moulding suits medium to large parts with moderate complexity.
Common materials used in compression molding include thermosetting plastics, such as epoxy, unsaturated polyester, and phenolic resins, as well as rubber-like elastomers, including natural rubber (NR), nitrile butadiene rubber (NBR), ethylene propylene diene monomer (EPDM), silicone rubber (VMQ), and fluoroelastomers (FKM).The process is also widely applied to fiber-reinforced composites, where reinforcements like carbon fiber or glass fiber are embedded into a thermoset resin matrix.Understanding the materials used in compression molding is key to evaluating its advantages and limitations in different applications.

Advantages and Disadvantages of Compression Moulding
Advantages of Compression Moulding
The advantages of compression moulding make it a preferred choice for many manufacturing applications. Its efficiency, versatility, and ability to produce robust parts highlight the compression molding benefits that drive its adoption across industries.
Cost Effective for Low Volumes Production
Compression moulding is economical for production runs of 100–10,000 units, balancing cost and scalability. Compression moulding reduces production costs through streamlined operations. The process requires minimal auxiliary equipment and simpler machinery. It avoids the high upfront costs of processes suited for mass production, making it a practical choice for small to medium batches.
Short Set Up Time
The advantages of compression moulding include rapid setup, with mould preparation taking days to weeks. Simpler mould designs and fewer components streamline the process, enabling manufacturers to launch production quickly. That rapid setup making it a standout compression molding benefit for prototyping and small-batch production.
Consistent Part Dimensions
Compression moulding can achieve consistent part dimensions. The uniform pressure applied during moulding ensures stable, repeatable dimensions across production runs, minimizing variations.
Excellent Surface Finish
The compression molding process produces parts with excellent surface finish. The mould’s smooth cavity and controlled curing process yield polished surfaces. This quality is ideal for consumer goods like kitchenware or aesthetic components, reducing finishing costs.
No Gates, Sprues, or Runners
Compression moulding eliminates the need for gates, sprues, or runners. Unlike injection moulding, material is placed directly into the mould cavity, simplifying production and reducing material waste from excess channels. This streamlined approach enhances efficiency and lowers costs.
Lower Tooling Costs
Unlike injection moulding, which requires complex moulds with gates, sprues, and runners, compression moulding uses simpler mould designs, significantly reducing tooling costs. The reduced complexity of mould fabrication ensures cost-effective production.
Low Material Waste
Compression moulding minimizes material waste. Precise placement of preforms or bulk compounds ensures only the necessary material is used, reducing excess. No gates, sprues and runners mold design also make the material waste lower in the mold parts.
Ideal for Large Parts
The process excels in producing medium to large parts, such as automotive panels or appliance housings, with consistent quality and strength. Its ability to handle sizable components without compromising structural integrity is a hallmark of the advantages of compression molding, making it ideal for industries requiring robust, oversized parts, from aerospace supports to industrial covers.
Simpler Process
Compression moulding’s straightforward mechanics—load, compress, cure—reduce operational complexity, a key compression molding benefit. This simplicity allows less skilled operators to manage the process and supports diverse applications, from consumer goods to industrial components.
High-Strength Parts
Producing durable, high-strength parts, especially with fibre-reinforced composites, is a standout compression molding benefit. Uniform pressure distribution ensures structural integrity, ideal for automotive bumpers or aerospace supports.
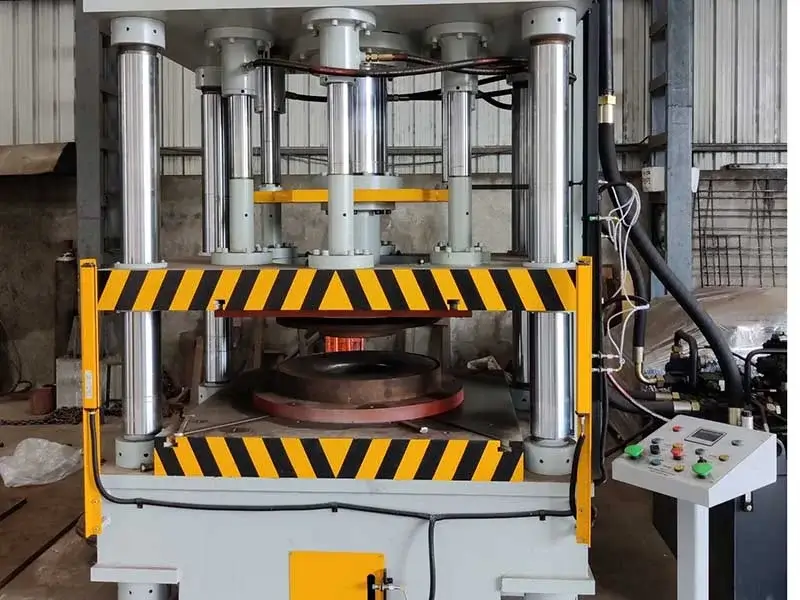
Disadvantages of Compression Moulding
While the advantages of compression molding are compelling, the disadvantages of compression moulding must be considered to ensure informed decision-making.
Not Suitable for Complex Designs
Compression moulding struggles with intricate geometries, such as micro-features, undercuts, or thin-walled sections requiring high precision (±0.005 inches). These designs risk defects like voids or uneven curing due to material flow and pressure limitations, making the process less suitable for highly detailed parts.
Longer Cycle Times
Cycle times of 1–10 minutes, compared to seconds for injection moulding, reduce efficiency for high-volume production. This slower pace, a key disadvantage of compression molding, Limits large scales production.
Higher Chance of Post-Molding Costs
Parts may require secondary finishing, such as trimming or sanding, for aesthetic or functional purposes, increasing costs. This need for post-processing, is a notable disadvantage of compression moulding.
Difficult to Control Flash
During compression molding, excess material escape the mould cavity to expel air, then produces thin, irregular protrusinons along the mould’s split line. That is the flash. It is a common defect in compression moulding and a notable disadvantage. Removing flash, typically from non-recyclable thermosets, requires labor-intensive trimming, increasing costs. Compared to injection molding, compression moulding’s flash is difficult to control and increase the post moulding finishing efforts.
Limited Automation Possibility
Manual material placement and mould handling restrict automation, leading to higher labour costs. Compare with automation potential of other processes, this limitation is a critical disadvantage of compression molding.
Applications of Compression Moulding
The compression moulding service widespread use across industries, leveraging its strength and versatility.
Automotive Industry: Produces durable, heat-resistant structural components, benefiting from high-strength composites. Examples: dashboards, bumpers, engine covers.
Aerospace Sector: Creates lightweight, robust parts for aircraft, utilizing the process’s ability to handle complex, high-strength composites. Examples: interior panels, structural supports.
Electrical Applications: Manufactures heat- and electrically-resistant insulators for high-voltage systems, ensuring durability. Examples: circuit breakers, transformer components.
Medical Devices: Delivers sterile, consistent parts for healthcare, capitalizing on precision and material versatility. Examples: surgical instruments, prosthetic components.
Consumer Goods: Crafts durable, customizable products with varied designs, leveraging cost-effective production. Examples: phone cases, kitchen utensils.
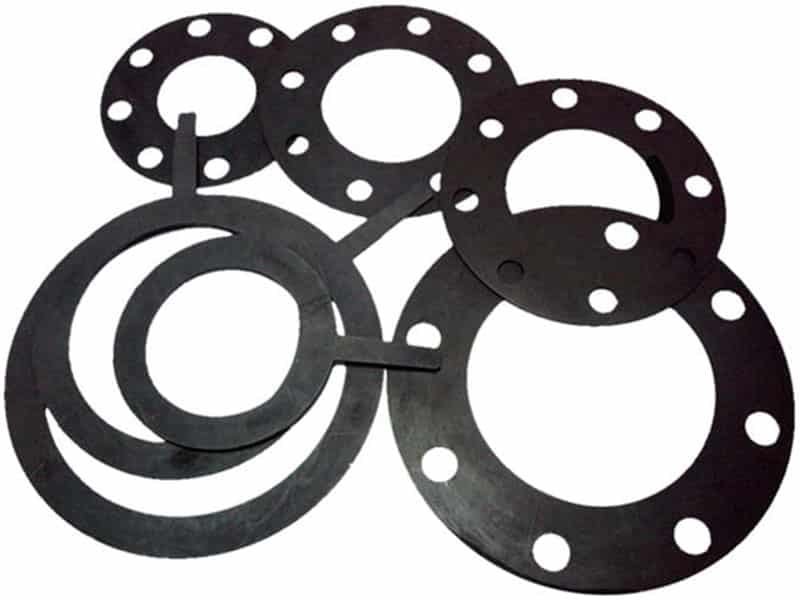
Conclusion
Compression moulding excels for projects requiring cost-effective, high-strength parts, particularly for medium to large components in low to medium volumes (100–10,000 units). Its advantages of compression molding—such as lower tooling costs, material efficiency, and robust performance—make it ideal for automotive, aerospace, and consumer goods applications. However, limitations like longer cycle times and challenges with intricate designs necessitate careful project alignment. Jiangzhi, a trusted leader in compression moulding services, offers expertise to optimize your manufacturing needs, from material selection to production. Embrace the compression molding benefits with Jiangzhi’s tailored solutions. Contact us to collaborate on your next project.